Cerium oxide is widely used in automotive catalysts. Ceria is thought to promote the water gas shift reaction, stabilize the alumina support, and stabilize the noble metal dispersion; however, its most important role is to act as an oxygen storage component . This property enables the catalyst to operate more ef®ciently by making it less sensitive to concentration variations that occur in the exhaust stream during normal driving conditions. Typically, as a catalyst ages, its conversion ef®ciency under transient conditions decreases in part because the ceria particles lose their ability to reversibly store and release (as CO2 or H2O) oxygen. One explanation for this loss in activity, is high temperature sintering of the ceria particles which renders the bulk of the ceria inactive for the Ce4 to Ce3 redox reaction. Another explanation for this loss in activity is that contact between ceria and the noble metals, which are known to promote the release reaction, is lost due to noble metal sintering. Due to the tendency to deactivate at high temperature there is a need for more thermally stable oxygen storage materials which can withstand temperatures at or above 9008C for long periods of time.
One approach previously used to stabilize ceria against sintering was to dope it with other rare earth elements such as La2O3 and Ga2O3; however, these materials did not prove to be signi®cantly better in fully formulated automotive catalysts. More recently, it has been reported that the addition of ZrO2 to ceria leads to improvements in ceria's oxygen storage capacity . The samples were usually characterized by temperature programmed reduction (TPR) and X-ray diffraction (XRD) and it was observed that the reduction of ceria was facilitated as the amount of Zr incorporated increased. XRD analysis showed that Zr was incorporated into the ceria lattice thereby forming a ceria±zirconia solid solution. In this earliest work, the preparation procedures used nvolved high temperatures (900± 15008C), resulting in highly sintered, and thus low surface area materials, making them undesirable as practical catalyst materials. Most recently, de Leitenburg et al. have reported that higher surface area materials can be formed by co-precipitation from cerium and zirconium nitrates followed by calcination in a temperature range between 827 and 11278C. Nunan et al. recently reported data on fully formulated Pt±Rh=CeZr=Al2O3 catalysts. The samples were evaluated using engine bench aging and testing. The authors correlated the improved performance of the Zr containing catalysts with the presence of a CeO2=ZrO2 solid solution; however, most of the details of catalyst formulation were proprietary, making it dif®cult to isolate and understand how the solid solution gives rise to better performance
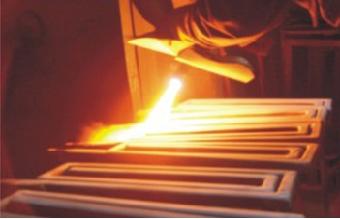
本文由桑尧热喷涂网收集整理。本站文章未经允许不得转载;如欲转载请注明出处,北京桑尧科技开发有限公司网址:http://www.sunspraying.com/
|