Plasma electrolytic oxidation (PEO) enables the growth of thick, ceramic coatings on valve metals, such as aluminium, magnesium, titanium and zirconium. The technology has been extensively explored to improve the wear resistance and corrosion resistance of aluminium alloys, often using silicate-based electrolytes. In contrast, aluminate-based electrolytes, which are commonly employed for treatment of titanium and zirconium have received less attention. Although PEO is a promising technique for developing high performance coatings, the high energy consumption and low coating efficiency are major impediments to commercial applications. Many approaches, such as modifying the electrolyte or the electrical regime, have been tried to address these issues. In a recent work,Matykina et al. reported that a pre-anodizing method can reduce the energy consumed in PEO of commercial aluminium alloys. The electrolyte composition has an important influence on the properties of PEO coatings. In our previous study on a 2A97 Al–Cu–Li alloy, coatings formed in dilute and concentrated silicate electrolytes were compared, showingmuch betterwear resistancewith a dilute electrolyte. The results suggested that incorporated silicon species are detrimental to thewear protection. The fact is not unexpected, since it iswell known that corundum, a crystalline form of nearly pure Al2O3, has an extremely high hardness, with a value of 9 in Mohs' scale of hardness. Hence, aluminate electrolytesmay have an advantage over silicate electrolytes for the development of wear resistant coatings by promoting the formation of α-Al2O3 (corundum) and γ-Al2O3 with respective hardnesses of 26 and 17 GPa. PEO coatings on aluminium alloys typically have lower hardnesses than α-Al2O3, usually in the range ~6–18 GPa. The few reports of PEO of aluminium alloys in aluminate electrolyte have usually employed dilute electrolytes (~7 g l−1 NaAlO2). In the present work, we show that extremely wear resistant coatings can be formed at high growth rates and with low energy consumption on an Al–Cu–Li alloy in a 32 g l−1 aluminate electrolyte. The wear resistance is associated with a high content of α-Al2O3, whilst the reduction in energy consumption and increase in growth rate are associated with the non-Faradaic formation of alumina. Plasma electrolytic oxidation of a 2A97 Al–Cu–Li alloy under a pulsed bi-polar constant current regime has been carried out in electrolytes containing 5, 32 and 56 g l−1 NaAlO2. Wear resistant coatings, containing relatively large amounts of α-Al2O3, were formed using concentrated solutions. The best protection was obtained with a relatively compact coating, generated with 32 g l−1 NaAlO2. The coating growth rate increased from ~1.5 to 11.3 μmmin−1 between 5 and 56 g l−1 NaAlO2. The high rates indicate that non-Faradaic processes contribute to the coating formation. Increased concentrations of NaAlO2 reduced the energy required for coating formation; e.g. to the range ~1 to 5 kWh m−2 μm−1 for coatings formed with 32 and 56 g l−1 NaAlO2.
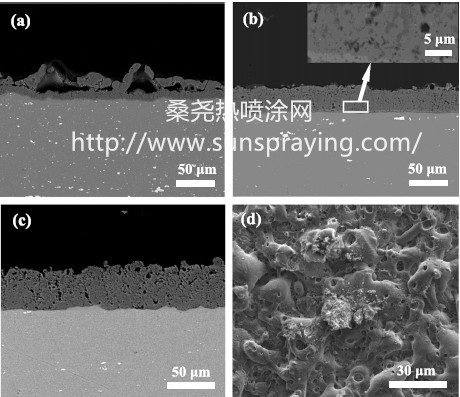
本文由桑尧热喷涂网收集整理。本站文章未经允许不得转载;如欲转载请注明出处,北京桑尧科技开发有限公司网址:http://www.sunspraying.com/
|