Bushan and Rusietto evaluated a number of foil and journal coatings, which in some cases, allowed operation to 650 ℃ but the coating life was limited. DellaCorte and Sliney have evaluated a chrome carbide journal coating in partial-arc bearing tests and found good performance but later difficulties were exhibited regarding coating reliability and high processing costs. These effort lead to the development of PS304 solid lubricant coating, which is a plasma sprayed coating using a powder mixture consisting of 10 wt% silver (as low-temperature lubricant), 10 wt% BaF(/CaF( (a eutectic, high-temperature lubricant), 20 wt% Cr2O3 (a hard, wearresistant phase) and 60 wt% NiCr (as a binder). The relative amounts of chrome oxide and nichrome in the coating have been optimized to provide coefficients of thermal expansion matching those of typical journal/shaft materials. PS304 has shown to provide low-friction and high wear resistance up to 480 ℃ when applied to rotating shafts running against foil bearings. Recent studies conducted by Kaur and Heshmat evaluated several experimental coatings for foil air bearings. Startup and shutdown tests were conducted on a coating test rig simulating journal foil air bearing performance for 500 start–stop test cycles using Inconel X750 top foil for the bearings against A2 steel as the journal coated with a dense chrome coating, at a load of 7 kPa. The foil coatings tested included molybdenum disulfide mixed with titanium nitride, titanium nitride, aluminum nitride mixed with titanium nitride, nickel, a ceramic based coating with molybdenum disulfide, a molybdenum based coating with graphite, a boron nitride based coating with graphite and polyamideimide. Friction coefficient, wear rate and surface roughness were determined and optical microscopy studies were conducted on each of the coatings after testing. The studies revealed that although the polyamide-imide based coatings exhibited a high coefficient of friction, they also demonstrated wear resistance, excellent adhesion and conformity to the surface. However, these coatings were not suitable beyond 260 ℃. The effectiveness of the soft coatings (polyamide-imide, molybdenum disulfide) in terms of low coefficient of friction was associated with the formation of an adherent transfer film on the mating surfaces. It was also found that the coating deposition method significantly influenced the surface topography, which did have a crucial effect on the tribological behavior during sliding. The coating thickness depended on the counterface material and the processing parameters and coatings with similar chemical composition but deposited by different methods exhibited different friction and wear characteristics. The optimum value for the coating thickness was found to be about 25 mm; coating thickness below this value lead to early film failure and thicker coatings lead to foil distortion and peeling effects. It was generally observed that coatings applied by the air gun spray process had better adhesion to the foil substrate as well as being the least expensive. These efforts lead to the development of a new series of Korolon TM coatings.
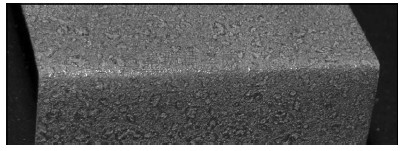
本文由桑尧热喷涂网收集整理。本站文章未经允许不得转载;如欲转载请注明出处,北京桑尧科技开发有限公司网址:http://www.sunspraying.com/
|