In order to highlight dominant wear mechanisms in axial pis to pumps, the authors performed an experimental multi-technical analysis on helicopter axial piston pumps [14]. The main wear mechanism I three-body abrasive wear between shoes and swashplate due to coarse carbides removal from the swashplate surface. Removed carbides an debris contaminate the hydraulic fluid and the other contacts. Carbide cause important wear in the other contacts that are not designed to bearsuch hard abrasive particles. In their case study on journal bearings, Ashby and Jones reported a similar mechanism of wear due t0 fluid contamination with silica. In their overview of fluid contamination in hydraulic systems, Frith and Scott highlighted the need for an appropriate filtration and an improved wear resistance in order to limit contamination effects. Wear causes in these axial piston pumps can be summed up in 3 problems that are the guiding thread of this study on wear resistance improvement: 1) Carbide removal results in fluid pollution and then in wear of other pump components. These carbides cannot be evacuated from the pump and the hydraulic circuitry because it is a closed system. Filtering cannot solve this issue either. There are different filters in the circuitry, however the carbides are thin enough (1–10 μm) to pass through them. Moreover, using thinner filter would result in filter clogging. 2) Bad lubrication and chemical compatibility can result in adhesion. 3) Wear resistance of most components is too low. A former study on wear in helicopter axial piston pumps showed the main wear mechanism in the contacts slipper/swashplate is abrasion due to carbides removal. Resulting debris and particles pollute the lubricating fluid leading to abrasive wear in most contacts. Accordingly, surface treatments on the swashplate steel are proposed to reduce slipper/swashplate wear. This study consists in a multitechnical experimental analysis of these solutions in dry and lubricated conditions. With lubricant, steel without treatment suffers carbide removal. PTFE coating prevents it by diminishing the coefficient of friction but are less resistant in highly loaded contact. Nitriding results in higher wear resistance, especially when lubricated. (DLC + WC) coating is the most efficient in dry conditions by minimizing friction coefficient and wear rate.
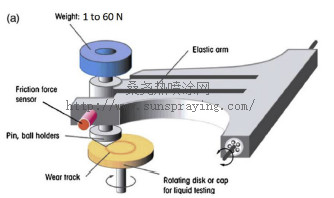
本文由桑尧热喷涂网收集整理。本站文章未经允许不得转载;如欲转载请注明出处,北京桑尧科技开发有限公司网址:http://www.sunspraying.com/
|