Axial piston pumps convert a motor rotation into hydraulic power. The motor rotation is transmitted to the barrel which drives piston-shoe assemblies, the ball-joint and the shoe-hold-down-plate (SHDP). A spring pushes the ball-joint on the SHDP which holds the shoes against the swashplate. As the shoes slide on the swashplate, its tilt forces pistons to translate in the cylinder bore and to pump fluid. The valve plate then distributes the fluid in the hydraulic circuitry. Hydraulic fluid fills the pump housing and acts as a lubricant. Piston/shoe and shoes/swashplate contacts benefit a better lubrication due to a hole in the pistons and shoes that lets a small amount of pressurized fluid out of the barrel. Although these pumps have a high power density and a relatively high efficiency, they have a limited life of few thousands hours due to wear of their components. Wear occurs in different forms and with different severities depending on the component. The resulting leakage flows are causing lower performances and reduced life. Consequently, wear in axial piston pumps interested some authors. Ma et al. adapted Zou's model to predict wear in the shoes/swashplate contact and compared their results to experimental ones. Wang et al. predicted the remaining useful life of an axial piston pump and monitored return oil flow to estimate global internal pump wear as a confirmation. These studies show a need to understand wear mechanisms in axial piston pumps but few wear analyses are performed on real axial piston pump components. Although some experimental multi-technical analysis of wear mechanisms in other systems can be found, this approach is still rare and lacks of application on axial piston pumps. On the one hand, there exists plenty of research on treatments and coatings. Some authors wrote reviews and studies on solutions that reduce friction or wear, such as surface texturing, solid lubricant coatings, or nanostructured coatings. Nesbitt proposes a list of suitable materials for pump design. More often experimental studies are conducted on solutions in order to access their wear resistance
and tribological properties. Tribometer wear tests are combined to characterization technics (SEM, XRD, 3D roughness, nanohardness, …) in order to highlight the effect of solutions on these properties. In the literature, two categories of studies are found. There are comparisons between close solutions. For instance, Lindquist et al. compare several Ti-based self-lubricating coatings, Özturk et al. compare nanocomposite nitride coatings. The second category gathers studies of the effect of a specific solution on one or several properties. However, comparative tests of multiple different solutions that solve a problematic or improve a specific property lack in the literature. On the other hand, some authors have studied the impact of one coated pump component on the corresponding contact wear resistance. Kalin et al. studied the influence on wear resistance of DLC-coated shoes by following wear evolution with optical microscopy and leakage monitoring. Lee and Hong focused on the effect of a CrSiN coating on the barrel surface in the contact barrel/valve plate. Their tests were performed on a customized tribometer. Brookes et al. studied the effect of changing the usual pump components materials for ceramic in the case of sea-water pump. The approach of these studies is closest to the one developed in this paper. Solutions are tested in order to improve pumps resistance and solve an industrial problem. Nevertheless, only one solution is tested. The step leading to this specific choice is not described.
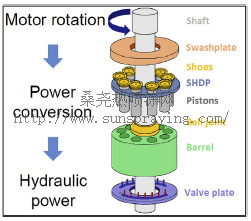
本文由桑尧热喷涂网收集整理。本站文章未经允许不得转载;如欲转载请注明出处,北京桑尧科技开发有限公司网址:http://www.sunspraying.com/
|