To overcome the bad corrosion protection behaviour, a new innovative coating concept was further developed by the authors, which is based on a TiN matrix coating by addition of a combination of magnesium (Mg) and rare earths (RE). The beneficial properties of a Mg addition to TiN in terms an improvement of the corrosion performance was already mentioned in. Here, the open circuit potential (OCP) of the TiMgN coating was reduced with increasing Mg content. The reduction in OCP by Mg alloying is very effective: Ti47Mg3N50 exhibits a quite noble OCP with +400 mVH (=voltage related to the standard hydrogen-electrode), while the OCP of the high Mg containing Ti24Mg58N18 is only −600 mVH. The authors refer the reduction of OCP by Mg addition as the “Mg-effect”. Taking advantage of this effect, the coating material is less noble, which should reduce the susceptibility to galvanic corrosion between coating and substrate. This hypothesis was approved in, where TiMgN coatings were deposited on the magnesium wrought alloy AZ31. Magnesium materials are generally challenging in terms of corrosion, because they exhibit a very low OCP and are very corrosive in the presence of NaCl. With TiMgN, a considerable increase of the corrosion resistance in the salt spray test could be achieved. Here, the coatings protected the corrosive AZ31 48 h against corrosion while conventional PVD coatings (TiN, CrN, NbN) already failed within several hours. In a next step, the corrosion performance of the TiMgN coatings was increased by a factor of 2 by application of HiPIMS. Since rare earth (RE) metals are known for the formation of very stable oxides and hydrophobic properties, which could improve passive film formation and re-passivation at defects, Gd was introduced in the TiMgN coatings by using Mg-30 wt% Gd target. With MgTiGdN, the corrosion protection onto Mg-AZ31 was increased to at least 200 h. The proposed mechanisms are on one hand, that Gd influences the surface energy and increase the water repellence capability (i.e. a hydrophobization). As a result, corrosive media are hindered to reach the corrosive steel at coating defect, thus significantly reducing the risk potential for galvanic corrosion. On the other hand, Gd addition promotes the formation of stable and dense surface layers or corrosion products, which effectively inhibit the corrosion kinetics at defects. The coatings exhibit a defect tolerance since, despite pinholes and droplets, there is no interface corrosion and spalling of the coating from the substrate, but resulting corrosion products “seal” the imperfections. The corrosion protection capability of TiMgGdN coatings was successfully approved for corrosion protection of mild steel. Here, the coated specimens withstood 800 h salt spray test without any significant macroscopic corrosion.The present investigations succeeded to the pilot studies by applying the TiMgGdN coating system to mild steel substrates, where the effect of the chemical composition and some deposition parameters on the corrosion performance was examined. Besides that, benchmark tests of the TiMgGdN coatings in comparison to established PVD-coatings, Si-DLC as well as electroplated Cr in terms of corrosion and wear performance were carried out. The present paper follows up to the studies, presented in. The effect of the several RE-elements on the corrosion properties is investigated. Also, a closer look was taken on the influence of the substrate materials' degree of purity regarding inclusions. Since the TiMgGdN should also ensure a sufficient wear resistance, a tribological benchmark was carried out. Today, innovative coatings must ensure wear protection and corrosion resistance for engineering materials with high corrosion susceptibility, e.g. mild steels, as well as the current sustainability criteria in terms of environment protection and health. PVD technology fulfils most of these demands, but unfortunately, the corrosion protection performance is unsatisfactory due to the typically low coating thicknesses of only few micrometres. One solution to overcome the corrosion problem are TiMgREN (RE =Rare Earth) based coatings, which were developed by the authors. Even with 5 μm thick monolithic TiMgGdN coatings a corrosion resistance of at least 800 h could be achieved in the salt spray test without any macroscopic corrosion attack. In the present work, the influence of the coating composition, the substrate material and the surface roughness on the corrosion properties was examined. Besides, the application of Gd as alloying element, the influence and the effect of other rare earth metals (La, Ce) on the corrosion performance were investigated. As benchmark, the TiMgGdN coatings were compared with industrial standard PVD coatings, DLC and electroplated Cr regarding the corrosion and the wear performance. The coatings were characterized concerning their microstructural, mechanical and chemical properties. Salt spray tests as well as electrochemical measurements were carried out to examine the corrosion properties of the coated specimens. Furthermore, ball on disk wear tests were conducted by reciprocal dry sling tests by using a SRV 3 tribometer.
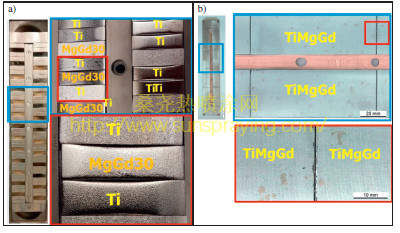
本文由桑尧热喷涂网收集整理。本站文章未经允许不得转载;如欲转载请注明出处,北京桑尧科技开发有限公司网址:http://www.sunspraying.com/
|