Protecting the surfaces of engine blocks made of Al-Si alloys with ferrous thermal spray steel coatings is an emerging tribological tech-nique that can be used to substitute for the traditional role of cast iron(CI) cylinder liners. Thus, the development of thermal spray coatings using plasma transferred wire arc (PTWA) or high velocity oxygen fuel (HVOF) techniques with low friction and wear is an important factor for the automotive lightweighting strategy. PTWA deposited coatings from an AISI 1010, 1020 grades or similar low carbon containing steel wire exhibit a characteristic lamellar structure consisting of ferrite splats delineated by oxide (FeO) layers. The surface of the engine bores should be resistant to sliding wear and scuffing under the unlubricated conditions that may arise during cold start or initial running-in periods. Thus, it is common to study the current and future engine bore materials under dry sliding contact and to examine the effects of counterface materials, surface textures and the role of coatings, including thermal spray coatings on the sliding friction and wear behaviour of powertrain components. The wear resistance of thermal spray steel coatings depends on the deformation behaviour of the splats [10,11], the fracture of the oxide layers adjacent to contact surfaces, and also the formation of oxide containing tribolayers. Laboratory tests were conducted to study the wear behaviour of PTWA low carbon steel coatings under different test atmospheres, applied loads and sliding speeds. Dry sliding performance of PTWA 1020 steel coated 319 Al alloy against a M2 grade high speed tool steel under the atmospheres with different relative humidity (RH) levels was investigated and it was found that the formation of hydrated iron oxides at the contact surfaces occurred at high RH and contributed to a low wear rate as well as a low coefficient of friction (COF). The role of surface oxides in dry sliding of PTWA 1020 coatings tested against a M2 steel was studied by constructing a wear map within a load range of 5–75 N and a sliding speed range of 0.2–2.5 m/s. At low speeds (≤1 m/s) and low loads (≤20 N) the oxidational wear that progressed by the formation of Fe2O3 was the dominant mechanism. At low speeds (≤1 m/s) and high loads (≥20 N), fracture of severely deformed ferrite splats adjacent to the contact surfaces was identified as the primary wear mechanism, which resulted in high wear rates. Oxidational wear mechanisms were also observed at high speeds but with different characteristics of wear debris consisting of a mixture of FeO, Fe2O3 and Fe3O4. Different types of iron oxides generated within the sliding contact surfaces may give rise to different wear properties. During fretting wear, a change of surface oxide com- position from Fe2O3 to Fe3O4 was detected using X-ray microanalysis, and a reduced wear loss was observed when Fe3O4 became the dominant constituent of the tribolayers. It was generally suggested that Fe3O4 could act as protective layers with strong adhesion to the sliding surface, whereas Fe2O3 layers may be removed from the surface more readily and the resulting debris particles may cause abrasive wear. Conversion of iron oxide phases on the PTWA 1010 steel coated Al-Si engine bore surfaces running against CrN coated piston ring was investigated during the course of dry sliding tests using in-situ Raman spectroscopy. At a constant load of 5 N and an average sliding speed of 0.02 m/s, Fe3O4 formation occurred on the spray coating surface after sliding for 140 cycles with an increase in COF up to about 0.40, and Fe2O3 was observed after 600 cycles with the COF stabilizing around 0.48.
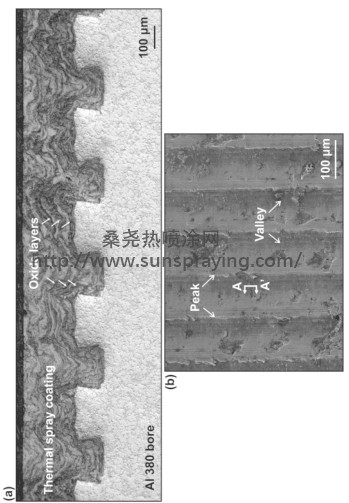
本文由桑尧热喷涂网收集整理。本站文章未经允许不得转载;如欲转载请注明出处,北京桑尧科技开发有限公司网址:http://www.sunspraying.com/
|