Studied the effect of oxygen-to-fuel ratio on the corrosion resistance of WC-CoCr coatings. They reported that increasing the oxygen-to-fuel ratio reduces porosity and this improves corrosion resistance. Montilisi et al. investigated the corrosion behavior of WCCo coatings in 3.5% NaCl environments. For this purpose, HVOF was applied to deposit, two grades of coatings of WC-12Co and WC-17Co with different coating thicknesses (0.05, 0.01, and 0.2 mm) on a plain carbon steel substrate using HVOF. They reported that by increasing the thickness of the coating layer it is possible to reduce the interlayer porosity and consequently increase the corrosion resistance of the coating. Wang et al. investigated the effect of adding chromium to WC-Co powder on the corrosion property of coatings and reported an improvement in the corrosion resistance of chromium-containing coatings (WC-Co-Cr). Considering the compressive stress caused by the peening effect, WC-Co coatings deposited by kinetic energy processes such as HVOF thermal spraying show better fatigue behavior compared to plasma spraying. Also, because particles are at a lower temperature and have less flight time, decomposition of WC to W2C, Co-WC, and other oxidizing phases is lower than thermal energy processes. Although WC-12Co coating is used mainly for its high wear resistance, it still can be considered as coatings even in severely corrosive environments. Bartkowski et al. studied the metal matrix composite coatings in the system of Stellite and tungsten carbides deposited by laser cladding. They observed that increasing the amount of WC causes an increase in micro-hardness of the coating with M7C3, M6C, and M23C6 carbides. A reduction in corrosion resistance in the coating was also observed with increasing the tungsten carbide content. Cobalt matrix carbides are favorite cases of wear and corrosion-resistant coatings. Among thermal spray processes the high-velocity oxy-fuel (HVOF) spraying is a popular choice because of its unique properties. In this paper the effect of particles’ temperature on the porosity, corrosion as well as wear behavior of high-velocity oxy-fuel (HVOF) thermally sprayed WC-12Co coating has been studied. The temperature of particles was measured using a Spray-Watch diagnostic system. Also the scanning electron microscopy (SEM), image analysis, and X-ray diffraction (XRD) were used for examining the powder and the coating. The corrosion potential and corrosion current density was evaluated using potentio-dynamic polarization test. Results show that the porosity is affected by thermal flow on the coating surface. Besides, a higher particle temperature resulted in achieving more amorphous phases and eventually the higher corrosion resistance. Sample A was coated with an impact temperature of 2012.4 °C. Although the porosity was higher than other sprayed samples (1.7%), the higher content of amorphous phase led to recording a higher corrosion resistance (64.3E-6A). Sample B was coated with an impact temperature of 1880 °C for which the Jcorr was 67.2E-6 A. Sample C was sprayed with a low impact temperature of 1702 °C for which a surface porosity of 1% and the low corrosion resistance of 79.5E-6A were recorded. Based on the experiments it was concluded that for the WC-12Co coating the corrosion resistant phases have the dominant influences on the corrosion resistance.
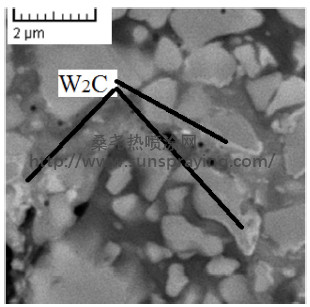
本文由桑尧热喷涂网收集整理。本站文章未经允许不得转载;如欲转载请注明出处,北京桑尧科技开发有限公司网址:http://www.sunspraying.com/
|