It is well understood that DLC coatings show low friction and high wear resistance at ambient temperature due to formation of graphitic tribolayer at the asperity contacts. The tribological behaviour of these coatings however is strongly influenced by the operational environment. Hydrogenated DLC coatings for exam-ple show higher friction with increasing humidity whereas lower friction is observed for hydrogen-free DLC (a-C and ta-C) coatings due to termination of the dangling bonds. Moreover with increase of the test temperature (100–300◦C), both graphitisation and oxi-dation of DLC coating degrade the coating properties leading to a substantial increase in both friction and wear coefficients. However DLC coating can survive comparatively higher temperature in the presence of lubricant, which isolates the coating from the hostile environment of the surroundings and acts as a coolant. The tribological performance at high temperature mostly depends on the test temperature, reactivity of the lubricant with the sliding surfaces (such as steel, DLC-coated, metal-doped DLC-coated,etc.), coating architecture and the coating deposition procedure. Therefore in high temperature applications (200◦C and above),it is imperative that the coatings possesses qualities like high thermal stability, strong coating–substrate adhesion, low coefficient of friction and high wear resistance. Furthermore it is important to understand that the coating and the surrounding ambient are two parts of one special tribo-system where the interplay between these two parts defines the overall tribologicalper for mance. Several approaches have been explored to achieve enhanced performance. tA molybdenum and tungsten doped carbon-based coating (Mo–W–C) was developed in order to provide low friction in boundary lubricated sliding condition at ambient and at high temperature. The Mo–W–C coating showed the lowest friction coefficient among a number of commercially available state-of-the-art DLC coatings at ambient temperature. At elevated temperature (200◦C), Mo–W–C coating showed a significant reduction in friction coefficient with sliding distance in contrast to DLC coatings. Raman spectroscopy revealed the importance of combined Mo and W doping for achieving low friction at both ambient and high temperature. The significant decrease in friction and wear rate was attributed to the presence of graphitic carbon debris (from coating) and ‘in situ’ formed metal sulphides (WS2and MoS2,where metals were supplied from coating and sulphur from engine oil) in the transfer layer.
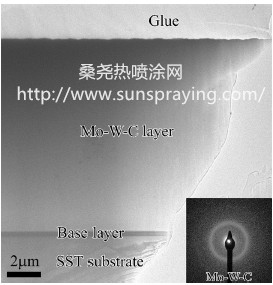
本文由桑尧热喷涂网收集整理。本站文章未经允许不得转载;如欲转载请注明出处,北京桑尧科技开发有限公司网址:http://www.sunspraying.com/
|