Solid self-lubricating coatings are primarily used to control friction and wear under severe application conditions, such as high vacuum, aerospace, high speeds, high loads, and very low or high temperatures, where conventional materials and lubricants cannot provide the desired performance or durability. At present, plasma spraying and laser cladding are two dominating and familiar surface technologies to fabricate solid self-lubricating coatings. However, the coating made by plasma spraying has high porosity, and the bonding between coating and substrate is mechanical. Laser cladding coating has some distinct advantages such as lower porosity, fully dense structure, minimal damage to the underlying substrate, and metallurgical bonding at the interface. Recently, increasing attention has been paid to laser cladding high temperature self-lubricating wear-resistant composite coating and it becomes one of the popular issues in the area of material surface modification. Yu et al. fabricated a self-lubricating wear-resistant NiCr/Cr3C2–Ag–BaF2/CaF2 metal matrix composite coating on 1Cr18Ni9Ti stainless steel substrate by laser cladding. It was found that the above coating had good friction-reducing and anti-wear abilities at room-temperature up to 500 ◦C. Wang et al. produced a self-lubricating wear-resistant CaF2/Al2O3 ceramic matrix composite coating on substrate of Al2O3 by laser cladding. The CaF2/Al2O3 composite coating has a unique microstructure consisting of Al2O3 primary phase and spherical CaF2 solid lubricant particles uniformly dispersed in the inter-framework regions. Compared with the laser clad monolithic Al2O3 ceramic coating, the CaF2/Al2O3 coating has much superior wear resistance and noticeably lower friction coefficient under dry sliding condition. Nevertheless, it should be noticed that as the solid lubricant, Ag is a noble metal and not suitable for large application. Because of its lower melting point (1270–1350 ◦C) and lower density (3.18 g/cm3), the use of CaF2 is also not easy due to its buoyancy, decomposition, vaporization and bad interfacial compatibility with the metal matrix. NiCr–Cr3C2 is a common cermet powder which has high hardness, anti-wear and anti-corrosion as well as anti-oxidation properties at relatively high temperature. The solid lubricant WS2 has the lamellar structure like MoS2 and graphite, and easy to be sheared, forming transfer lubricious films between the friction pair interface. In addition, WS2 has relatively high oxidation temperature (539 ◦C) than MoS2 (370 ◦C) or graphite (325 ◦C), so it can maintain lubricating property at relatively higher temperature. Therefore, in this paper, NiCr/Cr3C2–30%WS2 was designed to prepare high temperature self-lubricating wearresistant composite coating on Cr18Ni9 austenitic stainless steel by laser cladding. Phase constitutions, microstructures and dry sliding wear behaviors were investigated from room-temperature to 600◦C. Emphasis is placed on characterizing the high temperature wear behaviors and mechanisms as well as the functions of the addition of solid lubricant WS2.
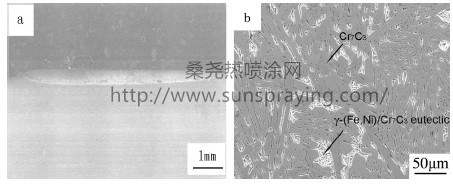
本文由桑尧热喷涂网收集整理。本站文章未经允许不得转载;如欲转载请注明出处,北京桑尧科技开发有限公司网址:http://www.sunspraying.com/
|