Traditionally, intensive research has shown that the poor tribological performance could be improved by introducing solid lubricants into ceramics matrix. Instructed by this concept, we have successfully fabricated self-lubricant mullite/graphite and ZrO2/ PTFE composite coatings. And they showed superior tribological performance under atmospheric environment. However, our follow-up studies showed that the above composite coatings lost their excellent tribological behaviors under high-vacuum conditions. The most likely reason was that the introduced lubricants (graphite and PTFE) are not suitable for high vacuum environment. Yen stated that carbon materials generally exhibit a high friction and poor wear-resistant ability under the environment lack of water vapor or oxygen. Harris et al. demonstrated that the existence of oxygen and water vapor is the necessary condition for the ultralow wear properties of PTFE/Al2O3 composites. Therefore, seeking for another suitable solid lubricant is an efficient method to improve the friction and wear behavior of thermal sprayed ceramic coatings under high-vacuum environment. Lamellar-like MoS2 is the best known and wildly used solids lubricant, especially in high vacuum environment or dry inert gas. Various methods can be used to prepare MoS2 or MoS2 based coatings, including sol-gel, physical vapor deposition, chemical vapor deposition, and magnetron sputtering. However, for thermal spray technology, it seems impossible to introduce MoS2 into ceramic coatings, because of the poor thermal stability of MoS2, including low oxidation temperature (< 400 °C), and decomposition temperature (~ 1300 °C). In other words, the ultra-high temperature of flame of spraying equipment would lead to the oxide or decomposition of MoS2. Thermal sprayed ceramic coatings have extensively been used in components to protect them against friction and wear. However, the poor lubricating ability severely limits their application. Herein, yttria-stabilized zirconia (YSZ)/MoS2 composite coatings were successfully fabricated on steel substrate with the combination of thermal spraying technology and hydrothermal reaction. Results show that the synthetic MoS2 powders are composed of numbers of ultra-thin sheets (about 7 ~ 8 nm), and the sheet has obvious lamellar structure. After vacuum impregnation and hydrothermal reaction, numbers of MoS2 powders, look like flowers, generate inside the plasma sprayed YSZ coating. Moreover, the growing point of the MoS2 flower is the intrinsic micro-pores of YSZ coating. The friction and wear tests under high vacuum environment indicate that the composite coating has an extremely long lifetime (> 100,000 cycles) and possesses a low friction coefficient less than 0.1, which is lower by about 0.15 times than that of YSZ coating. Meanwhile, the composite shows an extremely low wear rate (2.30×10−7 mm3 N−1 m−1) and causes slight wear damage to the counterpart. The excellent lubricant and wear-resistant ability are attributed to the formation of MoS2 transfer films and the ultra-smooth of the worn surfaces of hybrid coatings.
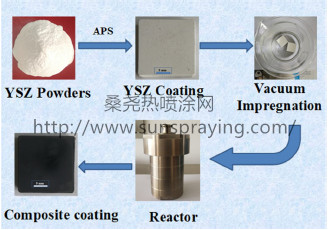
本文由桑尧热喷涂网收集整理。本站文章未经允许不得转载;如欲转载请注明出处,北京桑尧科技开发有限公司网址:http://www.sunspraying.com/
|