Nowadays, the design of self-lubricating materials is of great interest. There are different ways to prepare such materials, for example, there is a number of publications dedicated to the preparation of selflubricating alloys that have good tribological properties over a wide range of temperatures. For instance, the addition of sulfur to CoCrFeNiS0.5 high entropy alloy showed good tribological performances and allowed to reduce the antifriction coefficient from approximately 0.55 to about 0.41 at room temperature. The friction coefficient of the porous NiTi self-lubricating alloy with the storage of oil in the micro pores was decreased from 0.391 to 0.041. However, the production of such materials has disadvantages – a sintering temperature of 1100°C under vacuum and once the alloy is obtained, it is not possible to introduce the lubricating material one more time. There is a number of publications dedicated to the incorporation of lubricating particles into the material such as plasma electrolytic oxidation coatings with immersed PTFE particles. The incorporation of carbon nanotubes into nickel matrix composites allowed to reduce the friction coefficient to a minimum of about 0.13. Carbon nanomaterials such as carbon nanotubes, fullerene, graphene and graphene dioxide are also used for the preparation of self-lubricating materials. Deposition of graphene oxide via adsorption onto a 3-aminopropyltriethoxysilane (3-APS) nanofilm allowed decreasing the friction coefficient and the wear rate by 43.6% and 79.7%, compared to those of albronze lubricated by deionized water. Recently, the direction in self-lubrication of non-metal materials started to develop. Polymer materials tend to be damaging through cracks, that appear deep inside the material structure, where the detecting is complicated and repairing is almost impossible, and further exploitation of the construction is not possible anymore. In this case the particles that can reduce the friction coefficient are microcapsules loaded with lubricating agent. Epoxy coating showed anticorrosion and antifriction properties when loaded with polysulphone (PSF) microcapsules containing tung oil, as reported in. Here, the mean diameter of the synthesized microcapsules was approximately 130 μm. Tung oil-loaded PSF microcapsules were prepared by the solvent evaporation method. At a microcapsules content of 10 wt%, the lowest friction coefficient was 0.35, while unfilled epoxy showed 0.4. Double-layered isocyanate microcapsules with diameters of 80 ± 22 μm and loaded with 4,4′-bis-methylene cyclohexanediisocyanate (HDMI) lowered the average friction coefficient of an epoxy coating from 0.644 to 0.136. Polyurethane microcapsules containing a [BMIm]PF6 ionic liquid lubricant with a mean diameter of 43 ± 15 μm were embedded to epoxy coatings and lowered the friction coefficient to 0.151 at 30 wt% content of microcapsules in the coating. SiO2 solid particles wrapped by polystyrene microcapsules with diameter of 3.3 μm were incorporated in epoxy resin in an amount of 10 wt% which lowered the friction coefficient from 0.57 to 0.271.
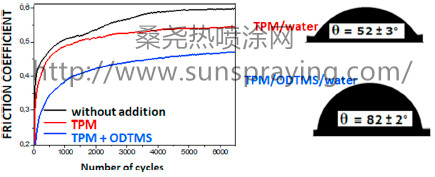
本文由桑尧热喷涂网收集整理。本站文章未经允许不得转载;如欲转载请注明出处,北京桑尧科技开发有限公司网址:http://www.sunspraying.com/
|