Hexagonal boron nitride (h-BN) has a lamellar crystalline structure which is similar to those of graphite and molybdenum disulfide (MoS2). This kind of structural properties of h-BN could be easily sheared along the basal plane of the h-BN and used as solid lubricant additives. Metal matrix h-BN lubricant composites are generally utilized in a form of coating or film instead of bulk composite because friction/wear always takes place on work piece surfaces. It has been used in different antiwear applications. Several surface coating techniques such as thermal spraying, electroless plating, and laser cladding have been reported for producing metal matrix h-BN composite coatings. I. Ozdemir et al. reported that FeB/h-BN coatings and Al-12Si/TiB2/h-BN composite were deposited onto an aluminum substrate by atmospheric DC plasma spraying to improve its tribological properties. O.A. Leon et al. reported that Ni-P-BN(h) coatings with thickness ranging from 7 μm to 20 μm were coated onto a AISI 316L stainless steel by electroless plating in a thermostatically controlled bath, and the composite Ni-P-BN(h) coating with an optimum BN(h) volumetric percentage of approximately 35% exhibits the best friction coefficient. Shitang Zhang et al. prepared Ni/hBN coating on 1Cr18Ni9Ti stainless steel substrate by means of laser cladding on a 10 kW transverse flow continuous-wave CO2 laser processing system. In our previous work, Co-based alloy/TiC/CaF2 self-lubricating composite coatings were successfully prepared on a Cr-Zr-Cu alloy for continuous casting mold by Nd:YAG laser cladding. In general, various surface modification techniques can be employed to produce composite coatings, among which laser cladding is very effective and offers distinct advantages such as lower porosity, improved microstructure and strong metallurgical bonding. Nano-Ni encapsulated h-BN/Ni-based alloy (Ni60) self-lubricating composite coatings on a medium carbon steel were fabricated by laser cladding using two types of lasers: a 5 kW continuous wave (CW) CO2 laser and a 400 W pulsed Nd:YAG laser, respectively. A high-energy ball milling method was adopted to clad nano-Ni onto nano-h- BN with an aim to enhance the compatibility between the h-BN and the metal matrix during laser cladding processing. The microstructure, phase structure and wear properties of the self-lubricating composite coatings were investigated by means of scanning electron microscopy (SEM) and X-ray diffraction (XRD), as well as dry sliding wear testing. The research indicated that laser cladding of the self-lubricating composite coatings demonstrates sound cladding layers free of cracks and porosities. It was found that a reaction between h-BN and Nibased alloy occurred, which generated hard phase CrB and Ni3B leading to the increasing of the microhardness of the coatings by CO2 laser cladding, while laser molten pool suppressed h-BN floating up to upper regions of coating for lower temperature and rapid solidification by YAG laser cladding. The high energy ball milling of nano-Ni onto nano-h-BN significantly improved the interfacial compatibility between h-BN and Ni60 matrix. The friction coefficient of the laser-clad Ni60/nano-Ni encapsulated h-BN coating was reduced obviously.
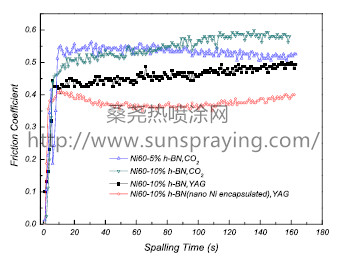
本文由桑尧热喷涂网收集整理。本站文章未经允许不得转载;如欲转载请注明出处,北京桑尧科技开发有限公司网址:http://www.sunspraying.com/
|