In recent years, self-lubricating wear-resistant coatings have rapidly advanced in modern industries, such as aerospace, automotive, food, and pharmaceuticals. The coatings were primarily developed in response to the needs of critical sliding components operated in harsh working conditions when traditional oil or grease fails. Currently, various surface techniques have been developed to produce self-lubricating coatings, i.e., plasma electrolytic oxidation (PEO), microarc oxidation (MAO), chemical vapour deposition (CVD), physical vapour deposition (PVD), thermal spray processing, plasma-transferred arc surfacing and laser cladding Among these techniques, laser cladding has gained particular attention due to its advantages, such as high quality, lower dilution of the coating, highly efficient process, a narrow heat-affected zone, and strong metallurgical bonding. In the fabrication method based on laser cladding, the main idea is to introduce the solid lubricants into the matrix with high wear resistance and build a metal matrix composites (MMCs) coating on the substrate by the melting deposition of the laser process. The secondary phase solid lubricants distribute in the matrix of the coating and play a role in friction reduction. Solid lubricants with a lamellar structure, such as graphite, transition metal sulfides, nitrides and fluorides, are the common medium for the lubrication additives of coatings, which easily form lubricative films between the friction antithesis interfaces. Many researchers have focused on fabricating selflubricating composite coatings using lamellar solid lubricants, such as CaF2, MoS2, WS2, and h-BN. However, previous research also found that lamellar solid lubricants are prone to ablation, decomposition and floating, as well as reaction with other components, when used as additives in laser cladding. Soft metals, such as Ag, Au, Sn, Pb, In, and Cu, can also act as solid lubricants and do not decompose . The good fluidity can drive the soft metal to repair the lubrication film by itself. However, a precondition of application in laser coating is that the soft metal cannot be dissolved or react with the coating matrix. In previous work, we fabricated a self-lubricating Fe-based composite coating containing Curich particles on nodular cast iron, which utilized the immiscible property between Cu and Fe. Torres et al. also prepared a selflubricating Ni-based composite coating with Ag/MoS2 inclusions on a stainless steel plate by laser cladding based on the immiscibility of the Ni-Ag system. However, the distribution and morphology of soft metal in the laser molten pool are affected by multiple factors, e.g., overcooling and convection. This property makes the soft metal prone to segregation in the molten pool, and the coating performance is difficult to control. These problems can be attributed to the incompatibility of manufacturability due to the differences in physical and chemical properties between the wear-resistant and self-lubricating components of the coating. There have been many attempts to overcome to these problems, such as encapsulating and in situ transition-metal dichalcogenide methods. Although these attempts improved the process to a certain extent, the fundamental issues are not fully resolved. This property may be related to the limited restraint or performance degradation involved in solid lubricants. A potential solution is to separate the manufacturing process based on the manufacturability of coating components, such as a double-layer composite coating. Han et al. reported a fabrication method of doublelayered composite coating to in situ fabricate Cu2S and FeS films by low-temperature ion sulfurization on the surface of Ni55 laser cladding coating. The double-layer method avoided the loss of solid lubricants during laser cladding, but the solid lubricating layer is easily consumed during the wear process due to a lack of adequate protection.
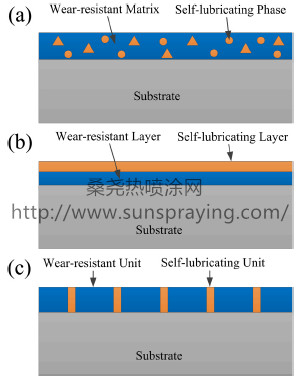
本文由桑尧热喷涂网收集整理。本站文章未经允许不得转载;如欲转载请注明出处,北京桑尧科技开发有限公司网址:http://www.sunspraying.com/
|