Titanium (Ti) alloys have been widely used in automobile, military, aeronautical, energy and biomedical industries attributing to their high specific strength, excellent corrosion resistance, and great biocompatibility. However, the durability and functionality of Ti alloys are limited by their relatively low hardness and hence poor wear resistance. Deposition of ceramic-based coatings is a promising surface modification approach to enhance the tribological performance of Ti alloy components. Commonly-used deposition techniques for ceramic coatings include thermal spraying, chemical vapour deposition (CVD), physical vapour deposition (PVD), and laser cladding etc. Thermal spraying is most widely used due to its capability of producing thick coatings of a variety of ceramic materials efficiently. However, thermal sprayed ceramic coatings often contain numerous micropores and microcracks, and the bonding of these coatings with the substrate is relatively weak. CVD and PVD are commonly utilized to deposit thin films and coatings with thickness in the range of 50 nm to a few micrometres, which may provide moderate level of protection against corrosion and wear, but cannot withstand severe mechanical abrasion. In contrast, laser cladding can produce dense and thick coatings (varying from 50 μm to 2 mm) with fine quenched microstructure, and excellent interfacial bonding. Therefore, laser cladding has been often used for depositing anti-wear coatings onto metal components. Despite of the apparent advantages of laser cladding, its application to deposit ceramic-based coatings faces two major challenges. First, high thermal stresses induced by rapid solidification can lead to cracking in the brittle ceramic coatings. Preheating of the substrate is considered as an effective approach to reduce the residual stress by significantly decreasing the thermal gradient and the cooling rate. For example, Wang et al. deposited crack-free Al2O3-13 wt.% TiO2 ceramic coatings on a Ni-based superalloy using a high preheating temperature of 500 °C along with optimum processing parameters. Besides, doping secondary ceramic phase could toughen the ceramic coatings. Ouyang et al. found that the addition of 2.5 wt.% TiO2 into yttria stabilized zirconia (YSZ) led to reduced and controlled microcracking in the laser-cladded coatings, which could potentially extend the service life of the coatings under conditions that involve thermal cycling. Second, considerable mismatch in the mechanical and thermal properties, particularly elastic modulus and thermal expansion coefficient, between a ceramic material and the base metal often induces stress at the interface, consequently leading to crack formation or even interfacial delamination. To mitigate the mismatch at the coating-substrate interface, various approaches were proposed including the application of a superalloy bond coating between the ceramic coating and base metal, the utilization of ultrasonic vibration during the laser cladding process, and the deposition of multilayer functionally graded coatings. However, the solutions mentioned above often involve supplementary devices and processes which are costly and time consuming. To solve this issue from a material perspective, TiO2 is selected to be the cladding material in this study due to its chemical similarity to Ti alloys, considering the compatibility of the coating and substrate material is crucial to achieve desirable metallurgical bonding. Also, TiO2 has been broadly applied to fabricate anti-wear ceramic coatings using thermal spraying, which exhibit high fracture toughness, bond strength and wear resistance. To the best knowledge of authors, few studies have been carried out on laser cladding of TiO2 coatings onto Ti-6Al-4V.
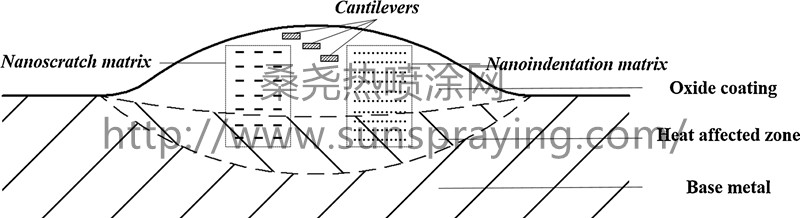
本文由桑尧热喷涂网收集整理。本站文章未经允许不得转载;如欲转载请注明出处,北京桑尧科技开发有限公司网址:http://www.sunspraying.com/
|