Gas turbine components need to resist high thermal and mechanical loads due to fuel combustion at high temperatures. Engine parts made of superalloys offer a wide range of service temperature and load capabilitie . However, in areas such as the combustion chamber or first-stage blades and vanes, gas temperatures are well above the service limits of Ni-based superalloys (i.e. >1000 ℃) . In order to enable the use of superalloys even beyond the service temperature limits, parts are coated by thermally sprayed thermal barriers to protect them against high temperatures and oxidation . To merge the ceramic top coat of a thermal barrier system with the substrate, an interconnecting bond coat layer is necessary: it enhances the adhesion of the ceramic top coat and provides oxidation protection to the substrate material. MCrAlYs, where M stands for Co or Ni, are the state of the art thermally-sprayed bond-coat materials used in turbine engine applications. In sections of the gas turbine where the thermal loads are lower, the ceramic top coat layer can be saved. For instance, blades and vanes in later stages of a gas turbine or in the compressor face gases at lower temperatures (e.g. 750 ℃), so for these blades or vanes, wear resistant and oxidation resistant coatings are commonly used. Wear resistance is especially important at blade tips, which run into an abradable layer on the inner turbine shroud for perfect sealing. Wear of the tip can result from hard ceramic phases contained in the abradable layer, and/or from foreign objects being trapped between the tip and shroud. These might be e.g. sand particles running through the gas turbine or fractured parts of failed TBCs. Other parts requiring wear protection at high temperature in a gas turbine include oil-free journal bearings, which operate above 500℃. Further examples of gas turbine components experiencing high-temperature sliding contacts are listed in Ref. Among the protective coatings proposed for such applications are those obtained by plasma spray processing of patented powder blends with NiCr or NiMoAl matrices, Cr2O3 hard phase and solid lubricants (metallic silver and fluorides). Those coatings, known as PS304 and PS400, exhibited good performance in lab-scale tests as well as in test rigs, but also some limits especially at temperatures above 750 ℃. Other promising coating candidates for the protection of gas turbine parts exposed to wear are aluminium oxide-dispersion strengthened (ODS) MCrAlYs due to their enhanced oxidation resistance and erosion resistance. In previous publications, some of the present authors have already explored the high-temperature sliding wear behaviour of NiCrAlY alloy coatings strengthened with fine Al2O3 or Al2O3 þ hexagonal boron nitride (h-BN). The coatings were obtained by a “hybrid” plasma spraying process, whereby the torch was simultaneously fed with a dry NiCrAlY powder and water-based suspensions of sub-micrometric Al2O3 and h-BN particles. Sliding wear losses in ball-on-disc tests at 700 ℃ approached the values obtained with High Velocity Oxygen-Fuel (HVOF) sprayed Cr3C2–NiCr. Since the NiCrAlY matrix also has advantages over Cr3C2–NiCr in terms of better oxidation and hot corrosion resistance, these coatings are particularly promising, but also reveal some drawbacks. Feeding the NiCrAlY matrix and the ceramic reinforcement separately allows for flexibility and lower costs, but bonding strength between these phases is limited. Manufacturing an ODS material is more expensive because of additional powder processing steps, but reinforcing phases are finer, more firmly embedded and uniformly dispersed in the matrix. It should also be possible to add more reinforcing phase than the maximum content of 18 wt% attained in Ref. The amount of hard phase can also be higher and its distribution more homogeneous than it can be achievedwith blends, such as it was done in Refs. At the same time, using an MCrAlY matrix should overcome any dimensional stability issues even at the highest temperatures.
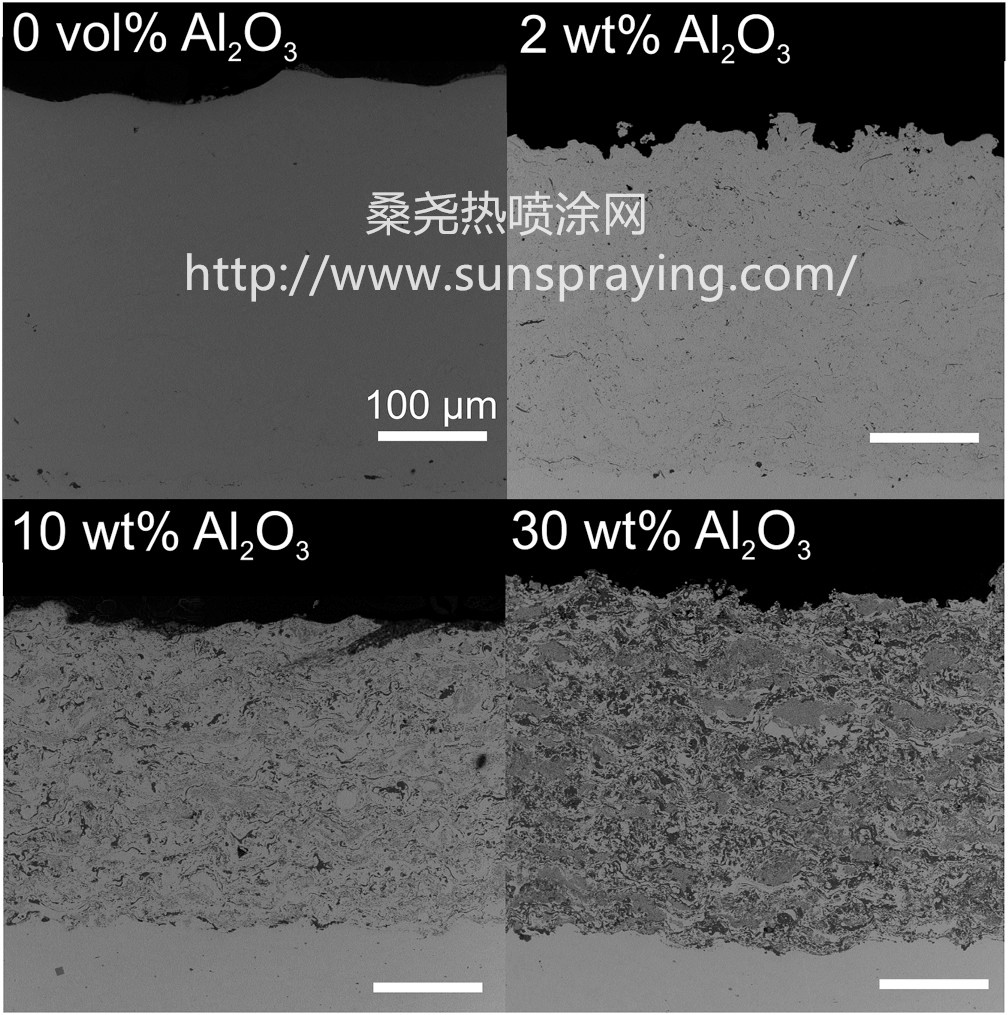
本文由桑尧热喷涂网收集整理。本站文章未经允许不得转载;如欲转载请注明出处,北京桑尧科技开发有限公司网址:http://www.sunspraying.com/
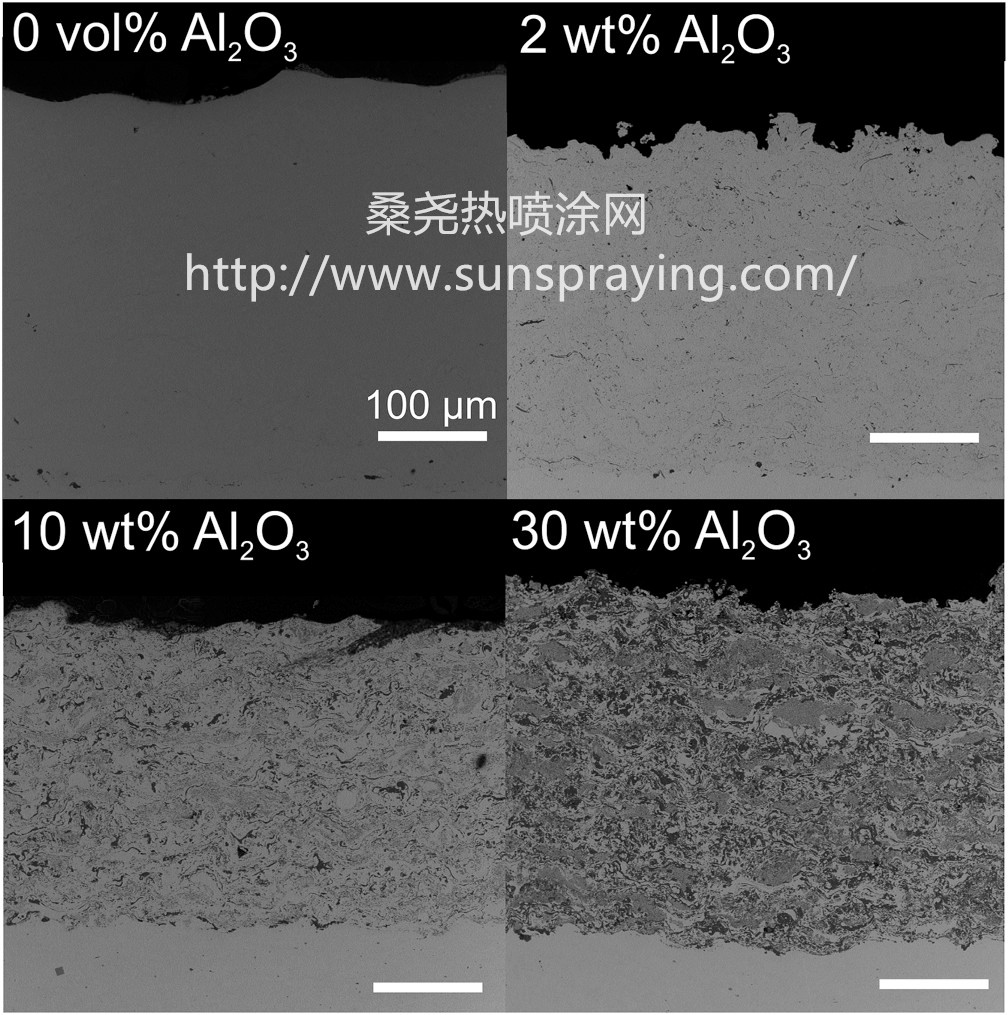
|