At the present time, TiC- or TiCN-based cemented carbides with Ni-Mo binder, or cermets, are widely utilized for the manufacture of indexable cutting inserts.Although these cutting materials have a higher brittleness and a lower thermal resistance than conventional WC-based cemented carbides with a Co binder, the cermets possess some unique properties including a high wear resistance, resistance to high temperature oxidation, and a low rate of interaction with iron-based materials, which allow successful utilization of these materials for semifinishing and finishing steel and cast iron, resulting in high quality of the workpiece surface being machined. There have been many attempts to improve the service lifetime of materials by means of deposition of wearresistant coatings which had been used in the cementedcarbide industry for WC-based cemented carbides. Although a number of both chemical vapor deposition (CVD) and physical vapor deposition (PVD) processes have been tried, there is no acceptable technology for the deposition of wear-resistant coatings on cermet cutting inserts and, usually, only uncoated cermet cutting inserts have been manufactured until now. Conventional CVD processes for depositing TiC, TiCN, TiN etc. coatings on the TiC- or TiCN-based cermets with the Ni-Mo binder cannot be utilized successfully because of an unfavorable interaction between the binder and the coating during the deposition processes. The TiC and TiN coatings deposited onto both the Ni underlayer and the TiC-Ni-Mo substrate contain a new phase and are crystallized in the form of coarse grains. The coatings are deposited in the form of dendrites or even needle-like crystals when the cemented-carbide substrate contains much Ni-based binder . These unfavorable changes in microstructure lead to a substantial decrease in the transverse rupture strength (TRS) of the coated cermets and the absence of improvement in the tool lifetime of the cermets after coating deposition. According to, the Ni Mo binder actively interacts with the TiC or TiN coatings deposited by the CVD process and the diffusion saturation process that results in formation of diffusional porosity in the coatings and surface layers of the substrate. The TRS of the coated cermets is less than half that of the uncoated cermets. The coatings include intermetallic phases of MoNi4 and Ti3Ni. The presence of other phases in the wear-resistant coatings leads to the appearance of high residual stresses in the coatings when cooling after deposition because of a substantial difference between the thermal expansion coefficients of the phases, which results in a shorter tool lifetime of the coated cermet inserts.
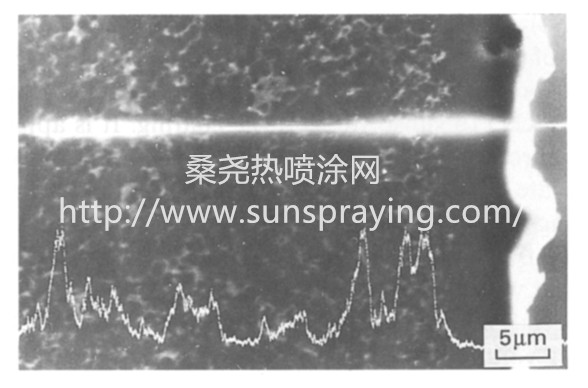
本文由桑尧热喷涂网收集整理。本站文章未经允许不得转载;如欲转载请注明出处,北京桑尧科技开发有限公司网址:http://www.sunspraying.com/
|