Shot peening is one of the surface modification techniques which improves the performance of materials under static, dynamic and cyclic loading. In particular the fatigue life, fracture toughness and wear resistance of materials could be enhanced significantly by this process. The fatigue strength, lifespan of chassis, springs, cam shafts and other automobile components are significantly enhanced by shot peening as reported by Wagner (2003). Recently, this process has been modified into a new technology called surface mechanical attrition treatment (SMAT). In contrast to shot peening the impact velocity and energy is high in SMAT so as to achieve severe plastic deformation of the surface. According to Dai and Shaw (2007) SMAT can be differentiated from conventional shot peening by larger strain, higher strain rate in the range of 103-105 per second and multidirectional repetitive loading. This kind of extensive plastic straining leads to grain refinement thereby it is possible to achieve a nano-crystalline surface. Wang et al. (2006) demonstrated that the grain refinement occurs via formation of dislocation cells, transformation of dislocation cells into walls and subgrain boundaries and subsequently into grain boundaries during SMAT. Lu and Lu (2004) the pioneers in SMAT have referred this process as self surface nano-crystallization of bulk materials and discussed its potential applications in designing novel materials and processes. The nanocrystalline surface created by SMAT consists of large number of grain boundaries and structural defects such as vacancies, dislocations, stacking faults, sub-boundaries etc. These defects acts as channels for atomic diffusion thereby reduce the activation energy for diffusion processes. A significant improvement in the diffusion kinetics is achieved by SMAT as a pretreatment by different researchers for nitriding, boronizing and chromizing. Tong et al. (2007) showed that the nitride layer thickness of iron pretreated by SMAT is twice as that of coarse grained counterpart in a gaseous nitriding process carried at 500 °C for 2 h. Tong et al. (2008) also demonstrated that effective nitriding could be performed on SMAT treated steel even at lower temperatures as low as 400 °C. Yao et al. (2016) reported that it is possible to boronize Ti-6Al-4 V alloy at much lower temperature (600 °C) if the alloy is pretreated by SMAT. It is also interesting to note that the surface toughness of this material is enhanced significantly while the hardness and coating thickness is equal to the coarse grained material treated at 1100 °C. Though there are many interesting studies the thermal stability of nanocrystaline surface is a limitation for diffusion processes especially, higher temperatures and longer durations. The application of surface mechanical attrition treatment (SMAT) in mechanical alloying of carbon into steel surface and its effect on microstructure and wear resistance of Ni-Cr-Mo Steel is investigated in the present study. The process is termed as surface mechano-chemical treatment (SMCT). A rotating wheel type shot peening machine with a provision for the supply of carbon is used for SMCT. Spherical shaped steel balls were used for mechanical attrition process and the carbon powders were fed continuously during the process so as to achieve mechanical alloying of carbon into the surface. Samples were obtained at the intervals of 15, 30, 45 and 60 min to investigate the changes in surface microstructure, hardness and tribological properties of the steel. The microstructures of the samples were studied using optical microscopy and SEM. The results clearly demonstrated mechanical alloying of carbon into the surface and formation of fine carbides by mechano-chemical reaction. The x-ray analysis also confirmed the formation of Fe3C by SMCT from α-Fe. The microstructure revealed the presence of layered nano-composite consisting alternate layers of ferrite and cementite (Fe3C). The fraction of carbide layers increased with process time while the grain size and layer thickness decreased continuously. This nano-composite layer altered the surface hardness and wear resistance of steel significantly. The surface hardness, increased exponentially with time and reached ∼950 HV0.1 after 1 h of SMCT. The rate of diffusion is determined using time and case depth up to which cementite formed by SMCT. The result showed about 1.524×1013 times higher than conventional thermo-chemical diffusion. A considerable improvement in wear resistance is also achieved by SMCT. The wear rate after 1 h of SMCT is 3.3 μm per km while it is 16.7 μm per km for untreated samples. The surface hardness and wear resistance of the steel is equivalent to that of conventionally carburized steel after 1 h of treatment. The rise in hardness and wear resistance could be attributed to the formation of hard Fe3C phases and nano-crystalline surface layer.
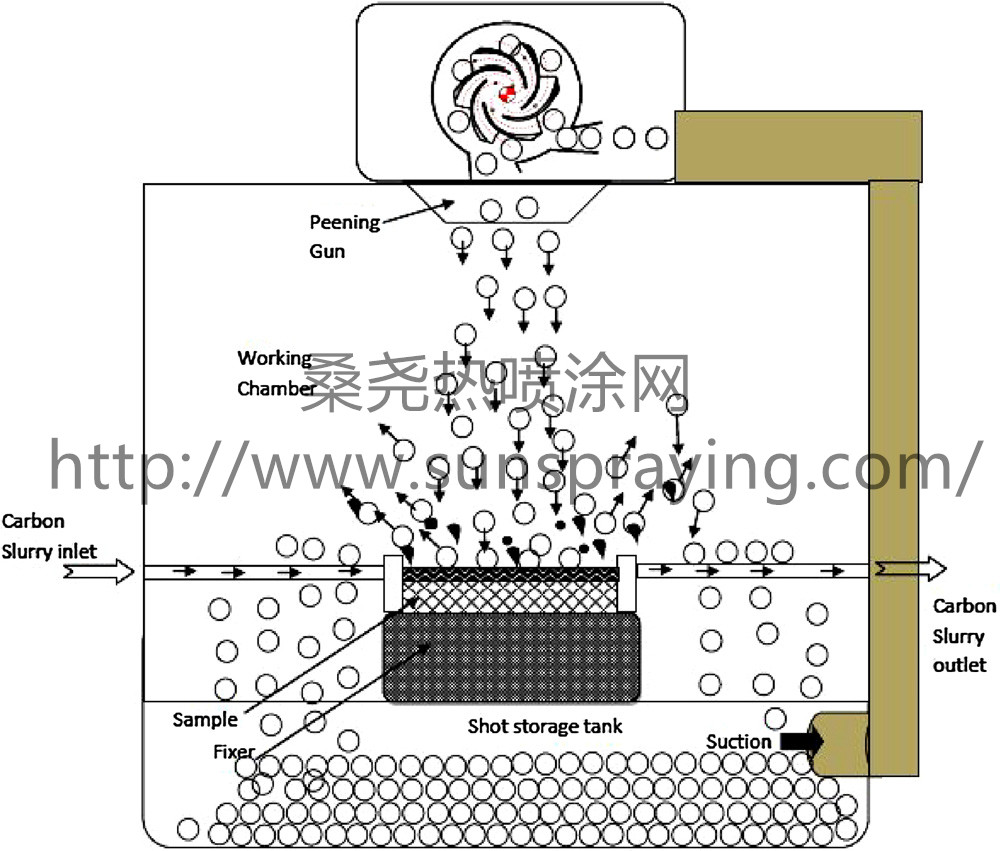
本文由桑尧热喷涂网收集整理。本站文章未经允许不得转载;如欲转载请注明出处,北京桑尧科技开发有限公司网址:http://www.sunspraying.com/
|