Magnesium alloys are gaining increasing attention for many industries day by day, as they show similar or even better combination of specific Young's modulus and high specific strength than many aluminium alloys and steels . However, their inherent poor corrosion and wear related surface degradation resistances are the main shortcomings limiting their wide spread commercial usage. In this respect, protection of the surfaces by a coating appears an attractive technical solution for enhancing the service performance and lifetime of magnesium alloys. Among the coating techniques, micro arc oxidation (MAO), which is an environmentally friendly electrochemical technique conducted at voltages higher than 200 V, is one of the most effective and economical method forming magnesium oxide (MgO) based coating having thickness ranging from 5 to 200 μm, depending on the process parameters and type of the electrolyte used . The electrolytes used in MAO processes are mainly alkaline based solutions containing silicate, phosphate or aluminate compounds. In general, aluminate-based (mainly NaAlO2) electrolytes are very attractive for fabrication of dry sliding wear resistant MAO coating on Mg alloys after process as they lead to formation of very hard (about 16 GPa) MgAl2O4 spinel phase within the coating. In this respect, increasing concentration of aluminate in the electrolyte increases the thickness and surface roughness of the MAO coatings, while providing enhanced tribological properties . However, MAO coatings synthesized in aluminate-based electrolytes show fairly less corrosion resistance as compared to coatings formed in silicate- or phosphate-based electrolytes . Thus, silicate- and phosphate-based electrolytes favour Mg2SiO4 and Mg3(PO4)2 phases, respectively, within the MAO coating and provide better corrosion resistance as they form passive layer inhibiting the corrosion attack . As an alternative to sole protection of magnesium alloys against corrosion or wear (in dry atmospheric conditions) by MAO coating, possibility of acceleration of wear depending on the presence of water on its surface (due to rain, dew, etc.) motivated the authors to fabricate MAO coating exhibiting excellent wear performance also in wet environments. For this purpose MAO is employed in mixtures of phosphate- and aluminate-based electrolytes (i.e. dual electrolyte) for benefitting from the positive contributions of phosphate- and aluminatebased electrolytes on the corrosion and wear resistances, respectively. Previously, Sheng et al. employed MAO in the mixture of aluminate- and phosphate-based electrolytes with some additives and determined the optimum composition of this dual electrolyte for formation of a compact, smooth and corrosion-resistant coating on ZK60 Mg alloy. Liang et al. revealed that utilizing dual electrolyte, consisting of phosphate and aluminate species for MAO of AM60B magnesium alloy, improved corrosion resistance along with a rough and coarse surface morphology. Likewise, Li et al. reported that MAO coating produced in a dual electrolyte, containing species of alumina and phosphate, exhibited high hardness and low friction coefficient while sliding against 2GCr13 steel disk as compared to AZ31 magnesium alloy. In a recent study, Yang et al. have reported promising tribo-corrosion performance for AZ31B magnesium alloy for biomedical applications upon combination of ultrasonic cold forging technology and MAO process employed in a dual electrolyte prepared by a mixture of aluminate- and phosphate-based electrolytes with some additives. In none of these studies our complementary approach for synthesizing corrosion-wear resistant MAO coating especially for wearrelated magnesium-based engineering components exposed to aggressive environmental conditions (such as salt poured on road or high humidity at the sea shore) has not been considered. It is suggested that our approach has potential to provide attractive technical solution for extending the utilization of magnesium alloys in manufacturing of engineering parts. This was initiated with the aim of extending the usage of magnesium alloys especially in corrosion and wear related engineering applications by coating their surfaces via micro arc oxidation (MAO). Considering the individual influence of phosphate-based and aluminate-based electrolytes on the corrosion and wear performances of the synthesized MAO coatings, respectively, AZ91 magnesium alloy has been subjected to MAO in aluminate-based reference electrolyte with and without additions of Na3PO4 at concentrations of 5 and 10 g/l. As opposed to dry sliding conditions, MAO coatings synthesized in the aluminate-based reference electrolyte did not provide good protection of AZ91 magnesium alloy against wear in corrosive media (0.9 wt% NaCl solution). This study revealed that, addition of 5 g/l Na3PO4 into this reference electrolyte was sufficient for enhanced resistance of MAO coating against chemical and mechanical degradations (i.e. corrosion-wear) without altering its features in terms of surface roughness and thickness.
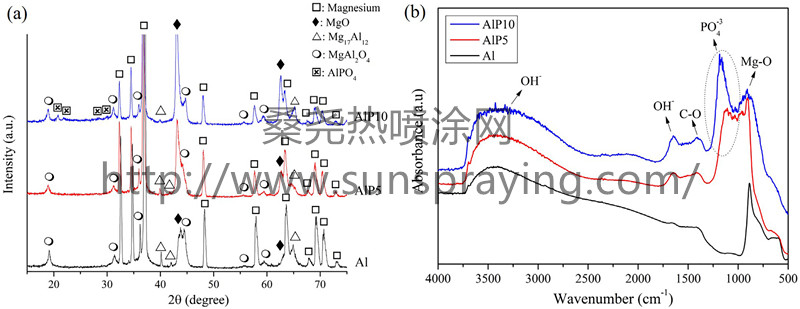
本文由桑尧热喷涂网收集整理。本站文章未经允许不得转载;如欲转载请注明出处,北京桑尧科技开发有限公司网址:http://www.sunspraying.com/
|