Industrial and aero gas turbines generally operate in places where small-scale solid particles, such as dust ingestion, are inevitable. “Small-scale” size of the erodent is defined with respect to that of the scale of the target material microstructure. These foreign small particles are carried by a fluid; consecutively impact on solid targets and cause material degradation. Turbine blades suffer from both WDE and SPE. Steam turbine blades are subjected to WDE (water droplet erosion) which caused by high energy impingement of liquid water droplets. Moreover, there is one of the important types of failure mechanisms, called solid particle erosion (SPE). Turbine components, especially blades and vanes, are designed to resist SPE due to reduce maintenance costs and increase service lives. SPE changes flow path by increasing roughness of the blades and vanes and decreases turbine efficiency. It may individually cause to fail the components or effect on fatigue strength as a secondary factor. Finnie proposed two major classifications of erosion mechanisms. Generally, SPE occurs in brittle materials, such as ceramic coatings, due to propagation and intersection of micro-cracks which have been initiated at the impact site. These materials present maximum value of material loss at normal angle of impact. In contrast, ductile materials, such as metallic alloys, are eroded due to severe local microplastic deformation at the impact site and show maximum material removal at low impact angles. Protective coatings are applied over the target surfaces to improve resistance of the surfaces against SPE. It is one of the effective methods with an easy acquirement. The application of erosion resistance by protective coatings has been experimentally and numerically investigated since at least 1980s. Nitride coatings such as TiN and TiAlN are applied on metallic substrates of blades and vanes by physical vapor deposition (PVD) to protect them against dusty environment and prolong their lives. PVD process is usually performed at temperatures below 500 °C. So, there is less risk of changing in substrate material properties during deposition of the coating. TiN and TiAlN are two typical types of erosion-resistant coatings broadly used in both cases of industrial and aero gas turbines. TiN is the only approved coating to use in aero-engines at least until 2007 due to restrictive requirements of aerospace industry and the predominant coating to resist erosion. Nevertheless, Titanium presents good affinity to TiAlN-based coatings due to high adhesion and mechanical properties of TiAlN coatings. Although monolayer coatings are extensively studied, recent researches demonstrated that architecture of coatings is an effective factor in resistance against wear; particularly erosive wear. The major defect of monolayer coatings is that they are quickly eroded by consecutive impact loads of erosive solid particles. Multilayer coatings with complex properties have been developed to solve this problem. Advantages in PVD with electron beam, magnetron sputtering and arc methods have opened more possibilities to make new coatings. Alternative layers with different properties can be designed to obtain an optimal architecture with better performance by improvement in fracture properties and impact strength. These architectures make it possible to deposit thicker coatings by relaxing residual stress. Mechanical properties of the multilayer coating systems can be changed by changing in number, sequence and other characteristic of the layers such as thickness and Young's modulus. In order to achieve an optimum design of wear-resistant coatings, it is necessary to conduct an efficient approach for determining appropriate protective coating architecture under various erosion conditions. This paper aims to investigate the multiple solid particle erosion failure of uncoated and coated Ti-6Al-4V alloy. To minimize the computational costs and time, this study presents a three-dimensional finite element model using representative volume element (RVE) technique for simulation of multiple solid particles impact. Johnson-Cook ductile damage and plasticity constitutive equations are used to describe high strain rate erosive behavior of Ti-6Al-4V. After verification of the present FE model, based on this model, the best architecture of Titanium-Nitride (TiN) based coatings deposited on Ti-6Al-4V alloy is numerically determined. At first, characteristics of the best monolayer TiN coating are obtained to use as a reference for multilayer configurations. Then, effects of thickness, Young's modulus and TiAlN layers on erosion resistance of the coatings are studied to optimize architecture of multilayer coatings. Finally, the optimized coating is deposited on Ti-6Al-4V alloy by physical vapor deposition (PVD) process and erosion behavior of coated and uncoated alloy is experimentally studied. Numerical results show that TiN/TiAlN coating is the best erosion-resistant coating compared to the other configurations of this study. It is made of a TiAlN bottom layer with 90% relative thickness and Young's modulus of 526 GPa and a TiN top layer with 10% relative thickness and Young's modulus of 300 GPa. An average 2.7 times improvement is experimentally obtained in relative erosion resistance for the coated alloy compared to the uncoated one.
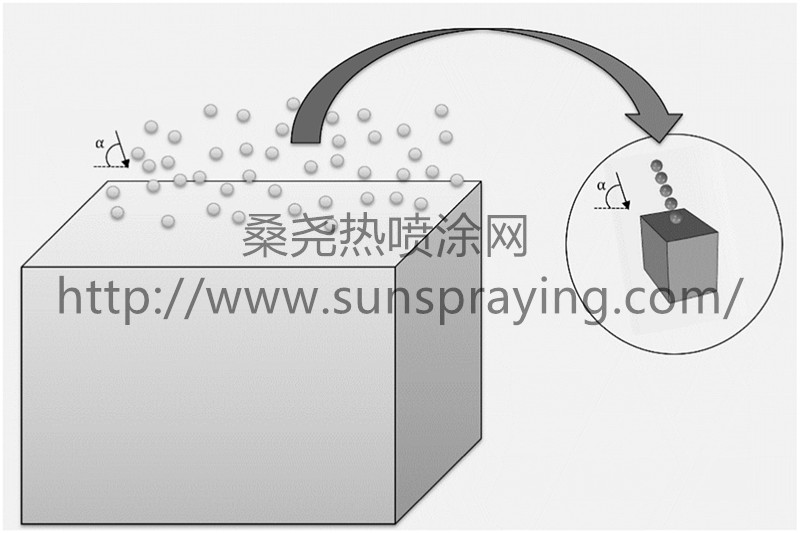
本文由桑尧热喷涂网收集整理。本站文章未经允许不得转载;如欲转载请注明出处,北京桑尧科技开发有限公司网址:http://www.sunspraying.com/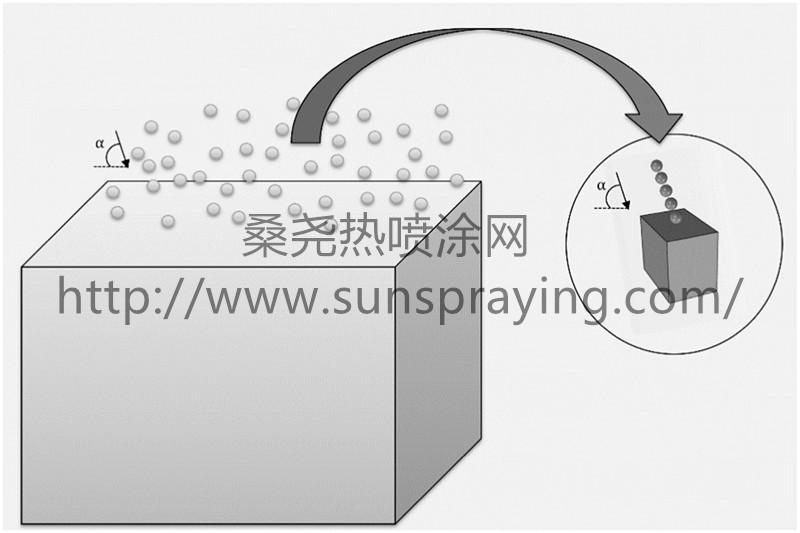
|