Thermal spraying is a process in which molten, semi-molten state or solid particles are deposited onto a substrate surface to form stacked layers for modifying the properties of the substrate . Three basic types of deposits including single-phase materials, composite materials and functionally gradient materials can be thermally sprayed. Due to the advantages, such as improved wear resistance, heat resistance, corrosion, oxidation resistance, etc., thermal spray is widely used in many fields. Vuoristo gave a description about the industrial applications of the coatings, such as HVOF-coated ball valve, ceramiccoated center press roll, section of gas turbine with abradable coating for clearance control, hip implants with thermally sprayed coatings and so on. Due to the complexity of surface of the large hull section, an optimization method adopting large spraying mechanical manipulator to ensure the coating thickness uniformity was proposed. Geoffrey et al. presented the PTWA process applied for cylinder bore coating which can reduce the friction coefficient. A kneader blade of injection molding machines was mentioned, which can be deposited coating to increase its surface wear resistance. In most of the high-value applications, coating components are usually very complex and in small batch. Thus, the research of coating deposition strategy for free-form surface is crucial. In the process of the thermal spraying, the spray gun trajectory has a strong impact on the quality of the surface coating. However, achieving a uniform coating on the spherical surface remains a challenge due to the complexity of surface with a large curvature. Especially when the spherical work piece to spray cannot be moved during the spray process, a well-designed robot trajectory is necessary to fulfill the coating quality requirements . Much work had been carried out on robot path planning for the free-form surface, such as the application of an external axis in robot-assisted thermal spraying and robot offline programming to elaborate coatings with enhanced uniformity. However, the existing method for free-form surface cannot solve the spherical surface coating problem well. In addition, current methods for freeform surface coating cannot achieve the accuracy requirements of special spherical surface coating. Thus, this paper proposes a new analytical thickness prediction model for spherical surface coating to improve accuracy, especially for nonholonomic spherical surfaces. Coating thickness prediction is critical for robotic thermal spray system's tool-path planning. Current prediction models could not give accurate estimation for a type of important spherical coating surfaces in industrial application. To facilitate tool-path generation and improve the coating quality for this special surface shape, this paper proposes a new analytical thickness prediction model. Both numerical simulation and experimental testing are conducted. The results reveal that the model is flexible and efficient to predict the coating thickness and uniformity in acceptable tolerance and expedient to predict the coating thickness on non-holonomic spherical surfaces. It could be used for automatic tool-path generation for the robotic thermal spray system. In this work, a method was proposed to predict the coating thickness, which was based on the spherical coordinates to develop the model of coating thickness on spheres with different scanning azimuthal angles. It can be considered as a basic model to generate an optimal robot trajectory in the future research. The Gaussian distribution was used to fit the coating profile. In order to enhance the uniformity of the coating profile, a trajectory for scanning moves alternately from the equatorial plane to the high latitude plane and from the high latitude plane back to the equatorial plane of the longitude at a constant acceleration has been introduced to generate path curves on the sphere. The model was confirmed by experiments, which was helpful to determine the optimal scanning azimuthal angle corresponding to an expected coating thickness and acceptable tolerance. Thus, the derived model is expedient to predict precisely the coating thickness on non-holonomic spherical surfaces.
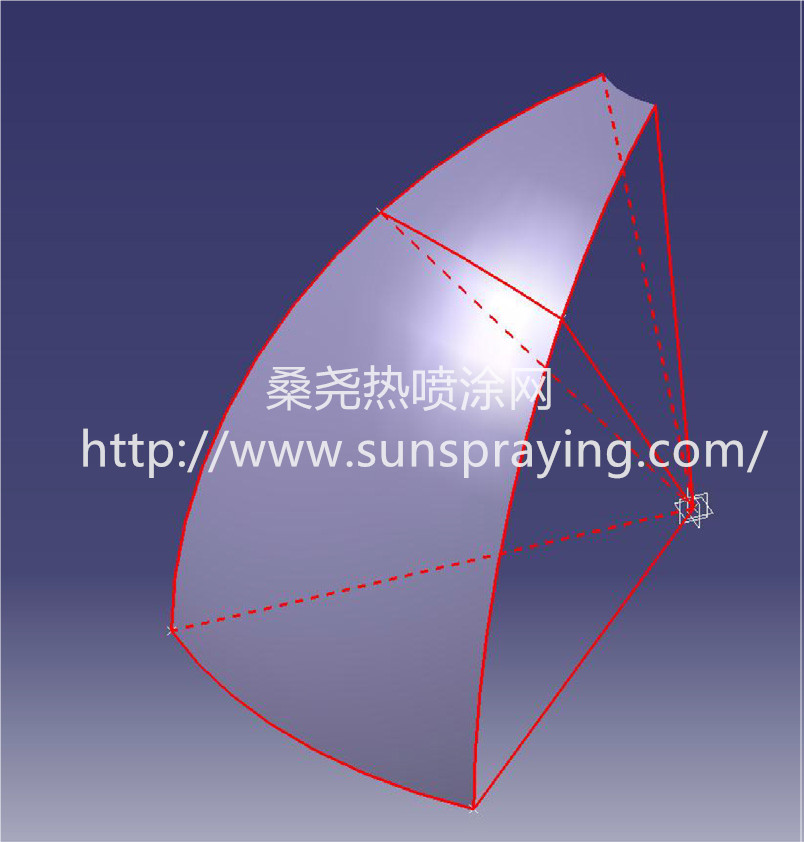
本文由桑尧热喷涂网收集整理。本站文章未经允许不得转载;如欲转载请注明出处,北京桑尧科技开发有限公司网址:http://www.sunspraying.com/
|