The 1020 carbon steel is widely used in the iron and steel material industry owing to its advantages of low price and high strength. It is commonly used for fabricating structural and mechanical components. The use of this steel can be further increased by subjecting it to suitable surface treatments. Iron and steel components are subjected to bending, wearing, rotating, or sliding loads at various sites. These components are not coated for maintaining their dimensional accuracy but are often plated with chromium at the loading sites to enhance their wear resistance. The use of chromium poses serious threats to human health and environment; thus, research is being conducted for finding alternatives to chromium plating. Tribology is the study of friction, wear, and lubrication of interacting surfaces between two moving objects. Friction is a major problem for almost all types of industries, as it causes wear, heat, and unnecessary energy consumption. The energy used to overcome friction turns into heat, and it is estimated that about 30-50% of the cost is that spent on replacing worn components. It is therefore very important to minimize the friction between moving parts. Frictional force is a resistant force that occurs when two contacting surfaces slide against each other, and it needs to be maintained at an optimum level to achieve a smooth and efficient operation of the machinery. The wear resistance of a coating can be improved by increasing the hardness, changing the chemical composition, reducing roughness and friction coefficient, and adding an appropriate lubricant. The wear resistance of a coating can be improved by chemical and physical methods. The physical ones include adding a solid lubricant at the interface between the two contacting surfaces to act as a buffer, and the lubricant will avoid direct friction between the two surfaces. The term ‘‘self-lubricating’’ indicates that characteristics can be reduced from the friction coefficient of a frictional surface without adding lubricant. The results of the wear test in this study indicate that the wear rate of Ni- MoS2 composite coatings reduced significantly without the addition of lubricant. This evidence suggests that HVOF Ni-MoS2 composite coatings are self-lubricating. The 1020 carbon steel is widely used in the iron and steel material industry owing to its advantages of low price and high strength. It is commonly used for fabricating structural and mechanical components. The use of this steel can be further increased by subjecting it to suitable surface treatments. Iron and steel components are subjected to bending, wearing, rotating, or sliding loads at various sites. These components are not coated for maintaining their dimensional accuracy but are often plated with chromium at the loading sites to enhance their wear resistance. The use of chromium poses serious threats to human health and environment; thus, research is being conducted for finding alternatives to chromium plating. Tribology is the study of friction, wear, and lubrication of interacting surfaces between two moving objects. Friction is a major problem for almost all types of industries, as it causes wear, heat, and unnecessary energy consumption. The energy used to overcome friction turns into heat, and it is estimated that about 30-50% of the cost is that spent on replacing worn components. It is therefore very important to minimize the friction between moving parts. Frictional force is a resistant force that occurs when two contacting surfaces slide against each other, and it needs to be maintained at an optimum level to achieve a smooth and efficient operation of the machinery. The wear resistance of a coating can be improved by increasing the hardness, changing the chemical composition, reducing roughness and friction coefficient, and adding an appropriate lubricant. The wear resistance of a coating can be improved by chemical and physical methods. The physical ones include adding a solid lubricant at the interface between the two contacting surfaces to act as a buffer, and the lubricant will avoid direct friction between the two surfaces. The term ‘‘self-lubricating’’ indicates that characteristics can be reduced from the friction coefficient of a frictional surface without adding lubricant. The results of the wear test in this study indicate that the wear rate of Ni- MoS2 composite coatings reduced significantly without the addition of lubricant. This evidence suggests that HVOF Ni-MoS2 composite coatings are self-lubricating. The discussion in the previous paragraph shows that only a few studies have been focused on thermally sprayed selflubricated coatings, and most of the feedstock powders for thermal spraying are prepared by pre-blend or mechanical alloys from which it is hard to form a uniformly dispersed composite coating. In this study, the wear resistance of thermally sprayed Ni-MoS2 composite coatings was investigated. The feedstock powders used in this study were Ni-MoS2 core-shell composite powders containing 25 wt.% dispersed MoS2. The powders were prepared by electroless Ni-plating technology, and the powder sizes were in the range 60-90 lm. The Ni-MoS2 composite coatings were subsequently fabricated by the HVOF process and were characterized by structural, surface morphological, and compositional analyses using microhardness tests, scanning electron microscopy/energy-dispersive spectroscopy (SEM/EDS), x-ray diffraction (XRD), and inductively coupled plasma atomic emission spectroscopy (ICP-AES). Ball-on-disk dry wear tests based on the ASTM G99 standard were performed at room temperature to evaluate the anti-wear properties of the coatings. Composite coating techniques are becoming increasingly popular owing to their peculiar performances. In this study, the wear resistance of thermally sprayed Ni-MoS2 composite coatings on an AISI 1020 steel substrate was investigated. Ni-MoS2 composite powder (size: 60-90 lm) containing 25 wt.% of dispersed MoS2 was prepared by electroless plating. Ni-MoS2 composite coatings were then prepared by HVOF thermal spraying. The coatings were characterized by structural, surface morphological, and compositional analyses by means of microhardness tests, SEM/EDS, XRD, and ICP-AES. For the evaluation of their anti-wear properties, the composites were subjected to ball-on-disk dry wear tests based on the ASTM G99 standard at room temperature. Experimental results showed that some of the MoS2 content dispersed in the Ni-based composite coating burnt away during the high-temperature spraying process, thereby reducing the MoS2 concentration in the coating. In the wear test, the weight loss in the Ni-MoS2 composite coating was minimal under a low load (<15 N) but increased rapidly with increasing load (>30 N). The average wear rate of the coatings was found to be ~1/40 times that of a Ni coating, showing that the wear resistance of the composite coatings was significantly improved by MoS2 addition.
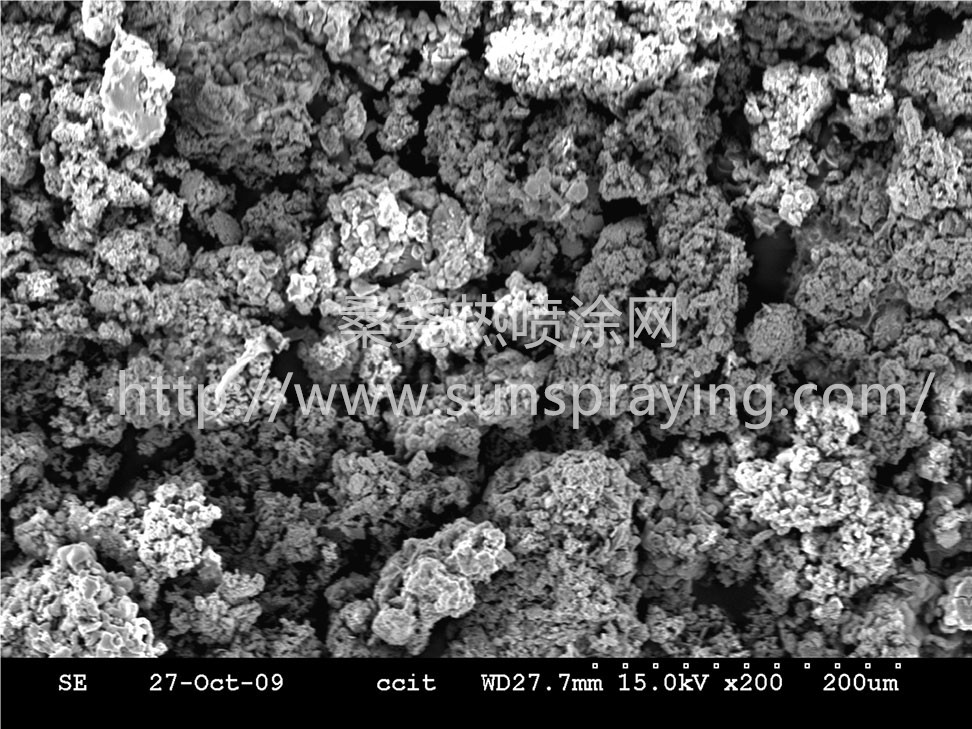
本文由桑尧热喷涂网收集整理。本站文章未经允许不得转载;如欲转载请注明出处,北京桑尧科技开发有限公司网址:http://www.sunspraying.com/
|