Nano- and submicron-structured iron sulfide self-lubricating coatings were produced by the HVOF thermal spraying method. Tribological tests showed that the thermal sprayed self-lubricating coatings not only exhibit a low coefficient of friction, but also showed excellent sliding wear resistance and high load capacity. This technique opens up a new way to make high performance self-lubricating coatings on components or parts, such as piston rings, cylinder liners, gears, heavy duty rear axle spiders, and rollers, especially parts working in difficult lubrication conditions. It is well known that friction and wear processes occur primarily at the surface of solids, as a result surface characteristics play an important role. The most important purpose for utilizing lubricants is to reduce friction and wear. For the operation of tribotechnical units in extreme conditions to be successful, it is necessary to develop special lubricated materials and methods. Sulfur is an important component in many organic and inorganic lubricants. The good lubricating properties of S compounds are derived, in our opinion, from the strong S-metal bonds formed at the surface. During mechanical contact, sulfide layers can thus prevent the formation of metal–metal bonds between the contacting bodies. Therefore, for solid lubricant films/coatings, the friction coefficient can be remarkably stable, despite the fact that much of the sulfide coating is worn early in the life of contact. The sulfides (such as MoS2) are layered-structure (close-packed hexagonal crystal lattice) solid lubricants, which have lubricating properties, especially at high load, high speed, or in a vacuum. Molybdenum disulfide (MoS2) is applied to surfaces by a number of methods, including simple rubbing or burnishing, air spraying of resin-bonded or inorganically bonded coating, and more recently, physical vapor deposition (PVD) techniques such as sputtering. Burnished films are the easiest and least expensive to apply, but have a very limited wear life. It is difficult to improve the friction and wear properties of resin-bonded spray coatings because of the influence of the bonding resin. In general, brush or spray painted coatings provide weak bonding to the substrate. Friction coefficients for sputtered MoS2 are about 0.01 to 0.15, but the thickness of the films is very thin, usually 0.1–1.5 lm. On the other hand, the apparatus is very expensive and the cost of production is very high due to the deposition procedure and conditions. Some work has shown that the durability of the MoS2 films depended largely on the type of sputtering apparatus used. Usually, thick films cannot be formed by use of sputter processes. Similar to MoS2, iron sulfide (FeS) also has a layered and close-packed hexagonal crystal lattice, making it attractive as an excellent solid lubricant, which has very good lubricating properties. The melting point of iron sulfide is 1188 ℃. A low-temperature sulfurizing method is currently under license from HEF France and is utilized in industry. This method (called the Sulf-BT process or Caubet process) is an anodic sulfurization performed in a suitable molten bath; its aim is the formation of a thin (a few microns thick) pyrrothite (Fe1)xS, a metal-deficient iron sulfide) film on steel. It has been shown that the FeS layer produced by Sulf-BT process not only separates the wearing surface from direct metallic contact as a solid lubricating layer, but also checks dynamic changes (i.e., reduce frictional temperature rising, plastically deformation, phase transformation etc.) in surface layers during sliding. As a result, the severe wear of steel specimens can be replaced by the mild wear of sulfurized samples. The load-carrying capacity is also improved by sulfurization. Therefore, the useful lifetime of parts can be extended.
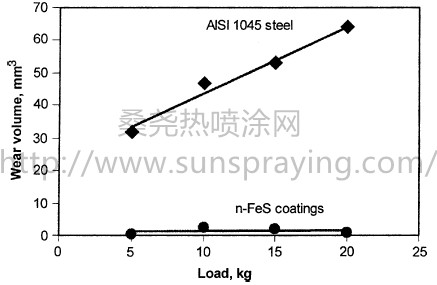
本文由桑尧热喷涂网收集整理。本站文章未经允许不得转载;如欲转载请注明出处,北京桑尧科技开发有限公司网址:http://www.sunspraying.com/
|