Electroless nickel has been used as a versatile material to protect from wear and corrosion. Its wear resistance has been well-established by suitable heat treatment and as a composite coating by incorporation of hard particles, i.e. SiC, Al2O3, etc. or lubricating particles, i.e. PTFE, MoS2, graphite etc. into the Ni–P matrix . Composite coatings, using electroless nickel as the matrix, have been applied in the surface finishing and engineering communities for many years. However, the coating hardness of electroless Ni–P composites is correspondingly decreased with the volume fraction of lubricating particles in the coating, and the friction coefficient becomes worse because of the hard particles. It has been found that hybrid composites reinforced with high-strength ceramic particles and soft PTFE exhibit better tribological properties than mono-particle-reinforced ones, owing to the cooperative effect of the respective advantages. Thus, it suggests a promising approach to producing Ni–P matrix hybrid composites with high wear resistance and low friction coefficient for wide applications. The investigations involved in hybrid composite coatings have been conducted by some specialists in recent years. Straffelini studied the surface durability of double coating Ni–P–SiC/Ni–P–PTFE composites. Y.S. Huang et al. discussed the microstructure and properties of Ni–P–PTFE–SiC. Additionally, Zhong cheng Guo submitted the studies on the wear resistance and the structure of electrodeposited Re–Ni–P– W–SiC–PTFE. Deng et al. submitted electrodeposited Re–Ni–W–SiC–PTFE composite and their properties. Few studies, however, were reported in the friction and wear behaviour of electroless Ni–P–PTFE–SiC composite, especially at high load. The dry friction and wear behaviour of Ni–P matrix composite with PTFE and/or Si Cparticles were investigated at high load. The wear resistance of the Ni–P matrix composites coincides well with the microhardness of each coating. Ni–P–PTFE exhibits the lowest friction coefficient and Ni–P–SiC has the lowest wear rate. At high testing load, Ni–P–PTFE–SiC presents the better anti-friction and wear resistance than other three Ni–P matrix composites. The PRMML formed on the worn surface is responsible for the good anti-friction properties and Si Cparticles mixed with PRMML plays a loadbearing role in protecting PRMML from shearing easily. A continuous supply of PTFE to the tribo-surface is an important precondition for the formation of PRMML and the exertion of its anti-friction properties. The low friction coefficient of Ni–P matrix with PTFE particles causes a little change of the temperature and further ensures the stable state of the whole sliding. Non-sticking and good chemical inert of PTFE make the surface of PRMML clean, and then avoid the severe adhesive wear and oxidation wear.
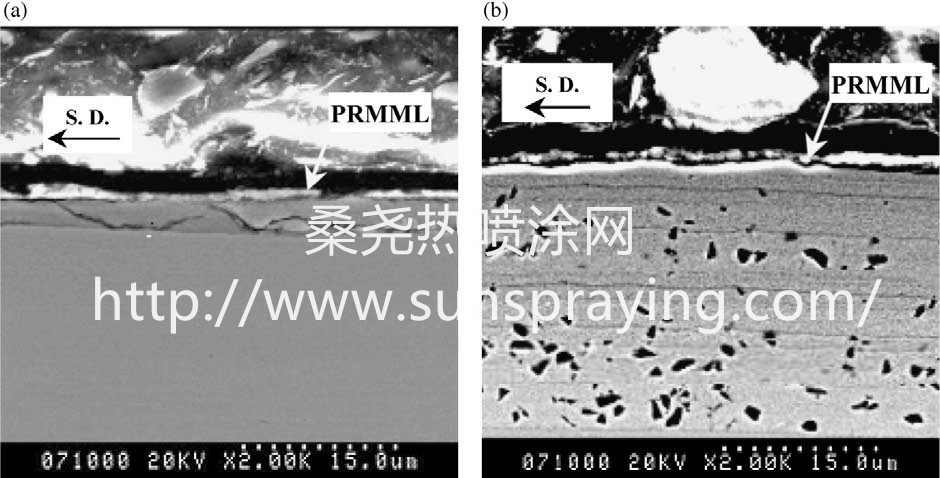
本文由桑尧热喷涂网收集整理。本站文章未经允许不得转载;如欲转载请注明出处,北京桑尧科技开发有限公司网址:http://www.sunspraying.com/
|