The use of lasers for creating defined textured patterns on surfaces has steadily gained attention during the past decade. These textures can contribute to friction reduction by acting as a reservoir for lubricant, hydrodynamic bearing and trap for wear debris. Surface texturing is a promising technique for improving the tribological properties of engineering surfaces. Arrays of dimples are deliberately created on surfaces by different techniques, such as laser ablation, etching or machining . Among them, laser surface texturing seems to be currently the preferred one for being inexpensive and readily available. Lasers used for texturing applications are able to create several surface patterns, such as dimples and grooves within a short time, making them a suitable cost-effective solution for improving the topography of engineering surfaces. An initial drawback of this technique was that during the melting and evaporation process of the ablated material, part of the material solidified at the borders of the ablated dimple, creating bumps. However, with the introduction of new pico- and femtosecond pulsed lasers for texturing applications, this effect can be avoided. Laser surface–textured titanium alloy surfaces coated with MoS2 were tested under reciprocating sliding at two amplitudes using a ball on flat configuration. The results showed that the COF can be significantly reduced when the texturing technique is used, especially for higher dimple densities, which provide more effective wear particles trapping effect. The COF was independent of the oscillation amplitude during the initial sliding cycles. Lifetime of the samples until coating failure depended on the testing conditions. For large amplitudes, surface texturing is a drawback. For smaller amplitudes, lifetime of the coating increased with the introduction of dimples, which effectively acted as wear particle traps. However, a dimple distance smaller than 50 lm was found to yield excessive contact pressure and low amount of MoS2 in the contact surface, causing negative results. Microscopy and XPS analyses of textured samples confirmed that the dimples below the contact area contain trapped wear particles and debris. For the testing amplitude of 0.5 mm, an optimum area density of dimples is found to be between 40 and 67 %. Afterwards, a sudden drop in lifetime is observed.
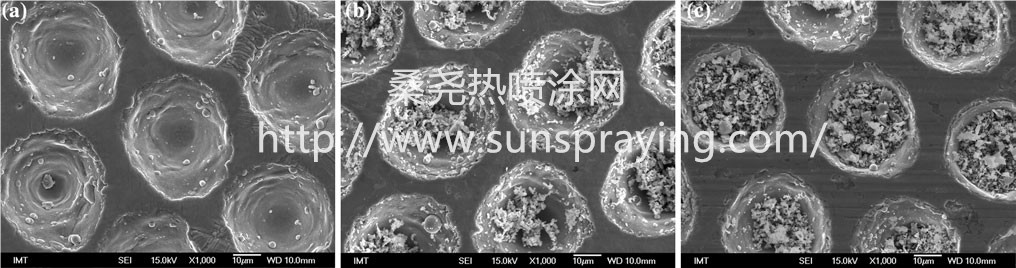
本文由桑尧热喷涂网收集整理。本站文章未经允许不得转载;如欲转载请注明出处,北京桑尧科技开发有限公司网址:http://www.sunspraying.com/
|