The development of today’s gas turbine engines has been the result of continual improvements in a wide variety of engineering skills including turbine design, combustion, and materials. One measure of the substantial improvements over the past five decades is the increase in the maximum gas temperature at a turbine airfoil afforded by these improvements. The increase in airfoil temperature has been facilitated by three principal materials developments: dramatic advances in alloy design to produce alloy compositions that are both more creep resistant and oxidation resistant; advances in casting technology that have facilitated not only the casting of large single-crystal superalloy blades and vanes but also the intricate internal channels in the blades to facilitate cooling; and the development of a viable coating technology to deposit a conformal, thermally insulating coating on turbine components. The advances and developments in the first two areas have been reviewed extensively elsewhere. Less well known is the development of thermal barrier coatings (TBCs), even though in the last decade their use has enabled a dramatic increase in airfoil temperature, far greater than that enabled by the switch from cast alloy blades to single crystal blades over approximately 30 years. As originally envisaged, the primary function of a TBC is to provide a low thermal conductivity barrier to heat transfer from the hot gas in the engine to the surface of the coated alloy component, whether in the combustor or the turbine (Figure 2). The TBC allows the turbine designer to increase the gas temperature, and thereby the engine efficiency, without increasing the surface temperature of the alloy. Subsequently, it has been recognized that a TBC also confers additional benefits, for instance, providing protection to rapid thermal transients such as occur due to flame out, and as a means to even out local temperature gradients. Indeed, in some cases, the use of a TBC has simplified the design of blades by minimizing thermal distortions of the blade. However, undoubtedly the biggest benefit of TBCs has been to extend the life of alloy components in the hottest sections in an engine by decreasing their surface temperatures.
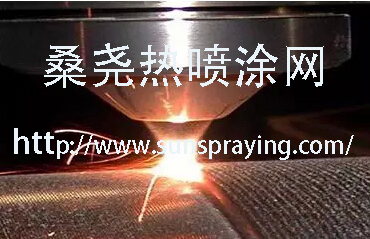
本文由桑尧热喷涂网收集整理。本站文章未经允许不得转载;如欲转载请注明出处,北京桑尧科技开发有限公司网址:http://www.sunspraying.com/
|