The enormous improvement in the wear behaviour of PVD-coated components is indisputable. However, PVD coatings are rarely used today for steel substrates, which are prone to corrosion, i.e. un- and low-alloyed quenching and tempering steels. Therefore, corrosion-resistant (and therefore expensive) substrates have to be used, which significantly reduces their economic efficiency compared to standard low-alloy quenching and tempering (QT) steels. The typical PVD-process related growth defects, e.g. pinholes or macroparticles (“droplets”), can act as paths where the corrosive medium penetrates down to the less noble substrate material. As a consequence of this, there is a high anodic current density due to the unfavourable electrode area ratios causing a rapid anodic dissolution of the substrate material. The difference between the corrosion potentials between the layer and the substrate determines the driving force for corrosion. In general, binary, ternary or higher-component nitride layers based on typical hard coatings like TiN or CrN exhibitmore noble properties than the low-alloyed QT steel substrates, thus accelerating corrosion kinetics by high anodic current densities at defects. Insulating coating materials such as Al2O3 or Si3N4 mitigate this problem. However, these layers are brittle and require special coating technologies, which are not common for job coating. Thick DLC-based coatings (> 20 μm) offer corrosion protection comparable to that of electroplated chrome, but with a hardness of only about 1000 HV these coatings are significantly softer than conventional DLC and require steels with a tempering temperature > 400 °C. Due to their low thickness, conventional DLC coatings are not suitable for the corrosion protection of low-alloy steels.In order to improve PVD coatings for applications under corrosive conditions, recent research activities have focused on optimizing the coating architecture as well as to reduce defects. By establishing multilayer systems, growth defects within a layer should not reach from the substrate to the surface due to the laminate-like structure. Hi-PIMS (High Power Impulse Magnetron Sputtering) could also produce denser and more homogeneous coatings with good adhesion and improved coating properties in comparison to conventional direct current magnetron sputtering (DC-MS). An improvement of the coating properties can also be achieved by a nanostructuring, e.g. by the addition of Si in order to increase the nucleus density and to limit crystal growth. Despite some successes in the laboratory scale there is no reliable PVD coating system available today, which shows a similar wear and corrosion performance as electroplated Cr. The main problem is the scaling effect between laboratory research and industrial application. In the laboratory scale, polished (“ideal”) specimens are common, which often deviate from the usual technical surface conditions. In most cases, even one critical pinhole in the coating is sufficient to cause corrosive failure of the component during operation.
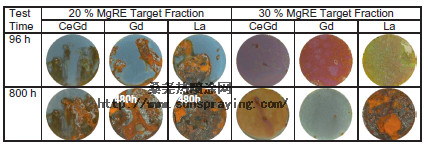
本文由桑尧热喷涂网收集整理。本站文章未经允许不得转载;如欲转载请注明出处,北京桑尧科技开发有限公司网址:http://www.sunspraying.com/
|