Protective, thermally sprayed coatings based on WC and a metallic binder are used extensively in various engineering applications to enhance the wear resistance of components. Major industrial applications require wear protection of core machine components and parts, which including utility boilers, air and industrial gas turbines, cylinders and rolls of paper machine, chemical and off-shore process components such as ball values, and aircraft landing gear axle. The components/parts have a significantly improved service life and could operate in harsh environment with the protective WC-based coating. For instance, the durability of HVOF thermal sprayed WC-17Co coated material under rolling contact fatigue (RCF) loading is 1.3 times the uncoated material (16MnCr5 steel). The WC10Co4Cr-based coatings have shown advantages over X20Cr13, X10CrNiMoV122, and Ti6Al4V to combat the steam turbine blades in water droplet erosion. Therefore, HVOF sprayed WC-based coating is a promising approach to solve the wear resistance related issues in various fields. WC-based thermal sprayed coatings are expected to withstand a broad range of loads, and to operate under temperatures up to approximately 500℃. These coatings exhibit high hardness (> 1100HV) and adequate toughness (> 5 MPa m1/2) as well as excellent the substrate (> 65 MPa in pull off tests). Currently the main commercially available compositions of WC-based powders are as follows: WC-12Co, WC-17Co, WC-12Ni, WC-17Ni, WC-10Co-4Cr, and WC-20CrC-7Ni (all compositions in wt. %). WC is typically used because of its high hardness and toughness as a ceramic whilst Co is the most widely used binder metal because it provides good wetting of the WC phase . Ni has also featured as a binder but appears to offer no more metallurgical and mechanical benefit over Co, except where the use of Co is not desirable due to the high cost and toxicity of Co, and the better corrosion resistance of Ni over Co. Many studies have been published on the sliding wear behaviour of WC-based thermally sprayed coatings. Thermally sprayed WC-based coatings typically comprise lamellar splats containing WC as well as to some extent W2C and W, in an amorphous or nanocrystalline metal matrix containing dissolved W and C. It is generally believed that the wear rate of these coatings is mainly a function of carbide particle size, the carbide content in the coating and the bond strength of the carbide particles to the matrix. It is also generally believed that reducing the amount of decarburization taking place during the thermal spraying process improves wear resistance. If large amounts of W and C dissolve into the metallic binder during the spraying process the binder becomes a complex multiphase alloy which can have low ductility. A high hardness of the binder is not necessarily advantageous but may in fact result in higher wear rates due to brittle cracking and fracture. On the other hand, if lower levels of W and C dissolution into the binder phase take place, the matrix may remain relatively ductile. However, a study by Sudaprasert et al. suggests that higher levels of decarburization produced with gas fuel spraying systems (due to hotter flame) may actually be beneficial to wear performance as less mechanical damage will occur during impact of powder particles with the substrate (as they have a higher degree of melting). Any mechanical damage is likely to result in higher levels of carbide grain fracture (and pull out) and hence higher sliding wear rates. Besides the WC hardening phase, Co as a binder phase could affect the wear performance of WC-Co coatings. For instance, it has been reported by Yang et al. for WC-Co cermets, that if this is the case, Co can form a thin layer at the interface between the coating and the counterbody which can act as a lubricant and therefore vastly reduce wear rates. There has been limited research of how Ni, Co or Co–Cr binders perform in relative terms. Yet, recent work by Younis convincingly shows that, in comparison with Co, a pure Ni binder leads to higher sliding wear rate and lower transition load from mild to severe wear when other factors are held constant.
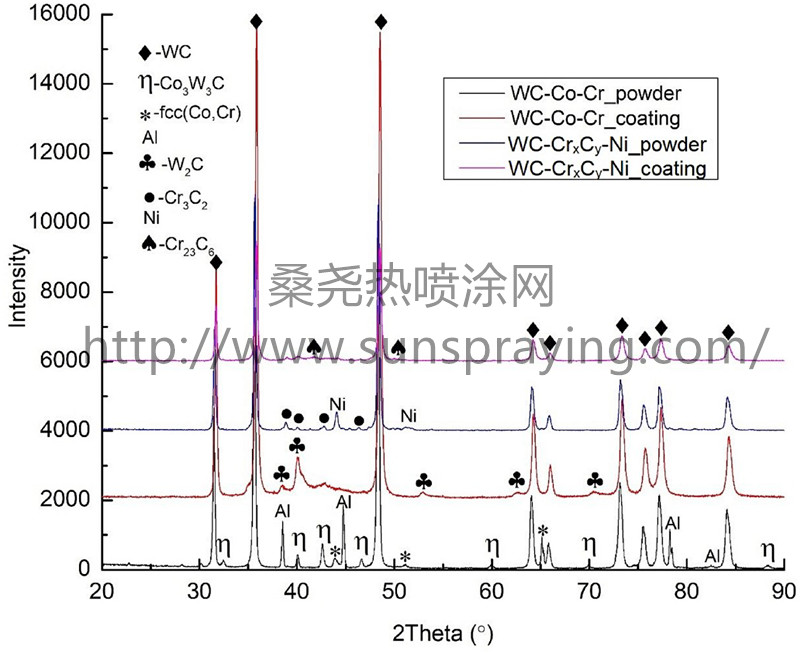
本文由桑尧热喷涂网收集整理。本站文章未经允许不得转载;如欲转载请注明出处,北京桑尧科技开发有限公司网址:http://www.sunspraying.com/
|