Solid lubricant systems were developed to provide friction and wear reduction in variable environmental conditions. The mechanisms employed to achieve cross-environment capability include “on demand” solid lubricant supply from reservoirs in hard wear protective coatings. This research explores recent advances in a precision laser machining to generate arrays of micrometer sized dimple reservoirs with controlled size, location, and density. These micro-reservoirs were machined by a focused UV laser beam on the surface of hard TiCN coatings produced by a cathodic vacuum arc deposition. Different dimple diameters and spacing were used to achieve area coverage with micro-reservoirs between 0.5% and 50% of the entire tribological contact surface. Solid lubricants based on MoS2 and graphite were then applied by burnishing and sputtering to such laser textured surfaces. Sliding friction tests were performed against steel balls in humid air and dry nitrogen environments. The results indicate that there is an optimum dimple surface coverage of about 10%. The life of the solid lubricants on dimpled surfaces was an order of magnitude longer than on the unmodified TiCN coating surface. The laser-processed micro-reservoirs also helped to renew lubricant supply for tests with multiple cycling between humid air and dry nitrogen. Tribological surface adaptation to the test environment was investigated by micro-Raman, which demonstrated a repeated change from hexagonal MoS2 to graphite carbon in the wear track with each dry/humid environment cycle. Solid lubricant composition inside the micro-reservoirs did not change.
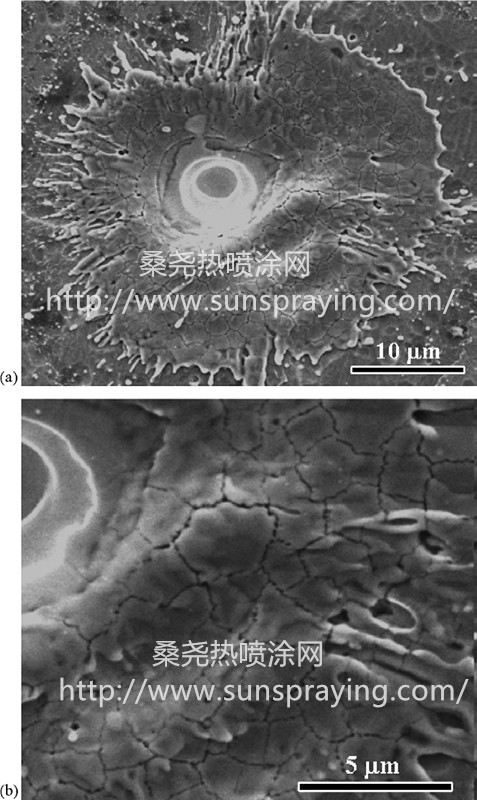
本文由桑尧热喷涂网收集整理。本站文章未经允许不得转载;如欲转载请注明出处,北京桑尧科技开发有限公司网址:http://www.sunspraying.com/
|