Ceramic coatings are potentially very effective in developing hard, wear-resistant protection layers on the surface of aluminium alloys. In the past decades, various surface treatments, such as chemical vapor deposition, physical vapor deposition, ion beam assisted deposition, and thermal spraying, have been applied to metallic substrates to improve their generally poor tribological properties. However, most of the methods mentioned above involve high processing temperatures, which may degrade the coating and/or substrate when forming alumina coatings on relatively low-melting point aluminium alloys. The microarc oxidation (MAO) technique can produce a thick alumina and other ceramic coatings on aluminium alloys at bulk material temperatures of less than 100 °C by plasmon discharge in an aqueous electrolyte solution on aluminium surfaces under high voltage. The ceramic coating yield can sharply increase the wear resistance of aluminium alloys. However, the ceramic coating produced also behaves as a high friction coefficient and has high surface roughness, which has limited the extensive engineering applications for MAO technology. Employing liquid lubricants may improve the tribological properties of the MAO coatings. While in rigid and severe working conditions, such as high vacuum, high temperature, chemical and radioactive environments, liquid lubricants often do not function. Because the MAO ceramic coating is formed on the metal surface via a series of localized electrical discharge events, there are many microholes left in the coating. This provides the probability to deposit small sized polymer into these microholes to form a binary coating. C.W. Yan et al. have explored depositing titanium organic polymers on the MAO coating to improve its corrosion resistance. Herein, we report a novel self-lubricating composite coating, Al2O3/ PTFE composite coating, which integrates the advantages of wear resistance of MAO coating and a low friction coefficient of PTFE polymeric material. It is confirmed that due to the porous structure of the MAO coating, PTFE can be deposited into it and form a compact film to cover the MAO ceramic coating via heat treatment. The MAO ceramic coating plays the role as the wear-resistant substrate, and PTFE film plays the role as the lubricant during the sliding. Compared with the single MAO coating, the yielded self-lubricating composite coating can sharply decrease the friction coefficient and wear loss during long-term sliding. Self-lubricating composite coating is fabricated on the surface of aluminium alloy, which integrates the advantages of wear resistance of microarc oxidation (MAO) ceramic coating and a low friction coefficient of polytetrafluoroethylene (PTFE). Inspection of SEM and EDS analysis indicates that PTFE can be deposited into the MAO coating, and a compact film forms which can fully cover the MAO coating. The yielded coating possesses superior tribological properties. The friction coefficient remains steady with minimal weight loss during long-term sliding.
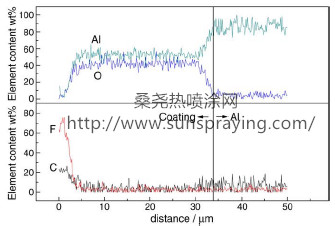
本文由桑尧热喷涂网收集整理。本站文章未经允许不得转载;如欲转载请注明出处,北京桑尧科技开发有限公司网址:http://www.sunspraying.com/
|