Modern aviation, aerospace, nuclear power and other high-tech industries are developing rapidly. More and more components need to work under extreme conditions such as high temperature, high speed and high load. The lubrication and wear resistance of these components are closely related to the reliability and life of the whole system. However, liquid lubricants are only suitable for environments below approximately 350 °C. Therefore, the demand for new self-lubricating materials with wide temperature range is imminent, and more and more researchers are paying attention to the research of materials with such properties. Solid self - lubricating materials are considered for use in wide temperature range self-lubricating. Soft metals are used extensively in solid self-lubrication such as Au, Ag, Sn, Pb, In, and Cu. Magnéli first discovered that transition metals can form substoichio metric compounds similar to MenO2n-1, MenO3n-1, and MenO3n-2, then the structural defects formed by these compounds form crystal shear planes, resulting in a decrease in bonding strength. A large number of researchers have focused on this performance to design selflubricating materials. Polcar et al. used a magnetron sputtering technique to prepare a WN coating. The W element in the coating was oxidized to form the WO3 phase, which played a good lubrication role . Suszko and Gassner et al. found that the sputtered MoN coating reacted with oxygen at high temperature to form MoO3 phase. The coating had a significant antifriction effect at 500 °C. However, the oxidation product MoO3 showed volatility above 500 °C, thus limiting the range of use of the coating as a solid lubricant. Fateh et al. prepared a V2O5 coating by magnetron sputtering. The coefficient of friction was found to be 0.55 at room temperature, 0.4 at 300 °C, 0.35 at 400 °C, and decreased to 0.15 at 600 °C. Wen Qin et al. studied Ta and TaCu coatings and found that the two coatings formed Ta2O5 phase during the friction process, which played a good role in friction reduction during the friction process. The ternary oxide coating was found to be a very promising alternative to the Magnéli phase of high temperature wear resistant materials. It has been found that the ternary oxide MexTMyOz has a relatively low friction coefficient of 0.1 to 0.3 at 350 °C to 900 °C, where Me is a precious metal and TM is a transition metal. For example, ternary oxides AgVO3, Ag3VO4, AgMoO3, Ag2MoO4 have a lower coefficient of friction of 0.15–0.25 at 500–900 °C. Silver tantalate is commonly used to study its dielectric properties and photocatalytic properties. Recently, it has been found that it has good self-lubrication properties at 500–750 °C. D. S. Stone et al. using solid-state synthesis technology to synthesize silver tantalite powder; magnetron sputtering technology to obtain a single silver tantalate film; adaptive cerium nitride/silver nano-sputter deposition coating to produce silver tantalate at high temperature. The friction and wear test at 25°C to 750 °C shows that the friction coefficient of AgTaO3 can be reduced to 0.06–0.15 at 750 °C. Hongyu Gao et al. used magnetron sputtering technology to make AgTaO3 films with Ag and Ta target on Inconel718 substrate. They used the Si3N4 ceramic ball as the friction pair and measured an average friction coefficient of 0.05 and a wear rate of 4 × 10−7(mm3 N−1 m−1) under a load of 500 nN and a temperature of 750 °C. They found that the experimental results were consistent with the MD prediction results of AgTaO3 friction and wear characteristics, and concluded that AgTaO3 has excellent self-lubricating properties at 750 °C. A comparison of friction and wear results from similar experiments is shown in Table. Laser cladding has many outstanding advantages: first, it has high energy density, fast heating and cooling speed to ensure the coating uniform and good microstructure. Secondly, coating and substrate are easy to produce epitaxial growth to form a good metallurgical combination and have a low dilution rate. Third, the formation of a large number of in-situ intermediate phase and the retention of non-melt strengthening phase are beneficial to improve the corrosion resistance and wear resistance of the coating.
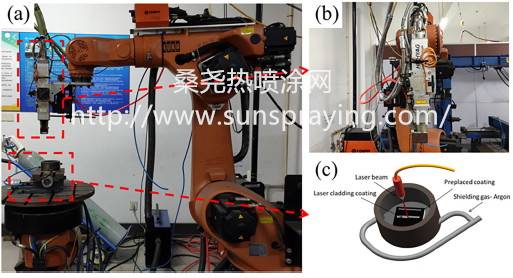
本文由桑尧热喷涂网收集整理。本站文章未经允许不得转载;如欲转载请注明出处,北京桑尧科技开发有限公司网址:http://www.sunspraying.com/
|