Plasma electrolytic oxidation (PEO), also often referred as to micro-arc oxidation and spark anodizing, is a method of ceramic coatings, typically 10 to 100 μm in thickness, on light metals of aluminum, magnesium, titanium and their alloys in aqueous electrolytes at ambient temperature . Highly crystalline oxide coatings are generally produced by PEO due to an exposure of coatings at high temperatures of more than 1000 °C at local and instantaneous microdischarge sites during PEO. Even though the coatings are exposed to high temperatures, the metallic substrates are usually kept at relatively low temperatures; no degradation of mechanical properties of metallic substrates occurs during PEO. Thus, the PEO coatings are promising for corrosion protection of aluminum and magnesium, wear resistance of light metals and their alloys, and improved biofunctionality of titanium . Ti–15V–3Al–3Cr–3Sn (Ti–15–3) is one of the practically used β- titanium alloys, with superior cold deformability in the β solution treated condition and a high mechanical strength after α phase precipitation aging. However, a main limit of this alloy is poor tribological behavior, characterized by high friction coefficients and severe adhesive wear. PEO is one of the promising techniques to improve the tribological behavior of Ti–15–3 by a ceramic coating. Recently, some of the present authors reported the PEO of Ti–15–3 in alkaline aluminate electrolyte, by which wear resistance was highly improved. A highly crystalline oxide coating, consisting mainly of Al2TiO5, was developed and the wear rate was reduced by many orders of magnitude after the coating. However, the coating was not highly adherent to the substrate. In the present work, two-step PEO of Ti–15–3, first in alkaline aluminate electrolyte and subsequently in acid electrolyte, has been carried out to improve adhesion of the wear-resistant coating. The PEO coatings developed in the present study have been characterized using X-ray diffraction, SEM and STEM with a particular attention paying to the structure of the coating/substrate interface for elucidating the adhesion of the coatings. Ti–15V–3Al–3Cr–3Sn (Ti–15–3) is one of the important practical titanium alloys with high cold deformability and high mechanical strength, but its wear resistance is poor. This paper reports the formation of wearresistant and adhesive ceramic coatings on Ti–15–3 by two-step plasma electrolytic oxidation (PEO). The PEO of Ti–15–3 has been carried out first in alkaline aluminate electrolyte to form a wear-resistant oxide layer and then in acid electrolyte containing both phosphoric acid and sulfuric acid to improve adhesion of the coating. The coating formed in the alkaline aluminate electrolyte is more than 10 μm thick, and highly crystalline. The main phase is Al2TiO5. This coating shows high wear resistance, but is not adherent to substrate due to the development of a number of voids and pores in the oxide layer close to the substrate. A new oxide layer with amorphous structure is formed next to the substrate in the subsequent PEO in the acid electrolyte, during which the voids are filled with a new oxide formed in the acid electrolyte, reducing the porosity. As a consequence, the adhesion of the coating is markedly improved without deteriorating the high wear resistance.
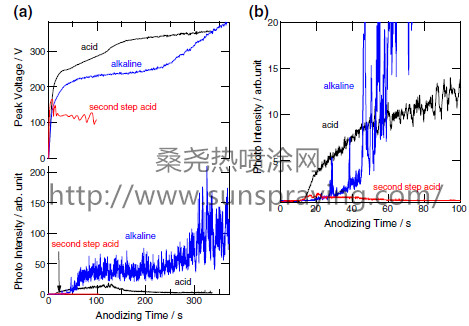
本文由桑尧热喷涂网收集整理。本站文章未经允许不得转载;如欲转载请注明出处,北京桑尧科技开发有限公司网址:http://www.sunspraying.com/
|