Titanium and its alloys have excellent characteristics such as low density, high specific strengthen, exceptional corrosion and oxidation resistance, good biocompatibility and mechanical properties. They are often used as structural components in the aerospace, petrochemical, marine industries automobile and biomedical fields . Among titanium alloys, Ti6Al4V alloy is mostly used as a general-purpose alloy. However, despite these numerous applications, it also suffers from the disadvantages of low surface hardness and poor wear resistance, which limits its usage under severe wear and friction conditions . In order to improve their surface properties, a lot of studies focused on studying the development of various surface modification techniques for preparing ceramic particle reinforced composite coatings in recent years. One of the most efficient approaches to enhance the tribological properties and expand the industrial application of titanium alloys is to fabricate a hard and wear resistant coating by laser cladding. As a promising surface-modification technology, laser cladding is widely used in many fields due to its high energy density, small heat input, small distortion, small heat affected zone, small workpiece deformation and metallurgical bonding with the substrate . Many researchers have prepared coatings to improve the wear resistance of titanium alloys. Farayibi et al. fabricated TiC+WC2+WC wear resistant composite coatings on the surface of Ti-6Al-4V alloys by laser cladding the powder of WC and the result indicated that the average microhardness of the composite layer is 678HV, which is approximately 1.7 times that of the substrate (396HV), and the wear volume of the coating is 7×10−5 μm3/μm, which is one-seventh of the substrate 4.9×10−4 μm3/μm). The composite layer has good wear resistance. Weng et al. produced the Co+TiN+Y2O3 composite coatings on titanium alloys by laser cladding. The average microhardness of the coatings was 1197.9HV0.2, about 3–4 times that of substrate, and wear rate of the coatings is 2.525×10−4 g/min, which is approximately 9.5–11.9 times that of substrate (2.995×10−3 g/min), an excellent wear-resistant coating is obtained. Tao et al. used laser cladding technology to prepare Fe and Ni reinforced the aluminum bronze coating on 316 stainless steel and found that the average microhardness of aluminum bronze coatings with the addition of Fe and Ni elements is 232 HV to 281 HV, which are higher than that of 316 substrate (180 HV). And wear weight loss of aluminum bronze coatings with different contents of Fe and Ni is 10.4, 5.9, 4.8, 6.5, 7.4 mg, respectively, which are less than that of 316 stainless steel (32.9 mg). From the abovementioned examples, it can be seen that those coatings were enhanced through increasing surface hardness. However, coefficients of friction of the above mentioned coatings have been ignored. High friction coefficients under severe working conditions (heavy load, high temperature, high pressure, etc.) will shorten the service life of friction pair . Therefore preparing a composite coating with excellent anti-wear and friction-reducing properties is an effective way to solve this problem. Titanium nitrides (TiN) have been proven to be effective reinforcements of titanium and its alloys. Their favorable properties include a high degree of hardness and excellent wear-resistance in numerous tribological systems. Many studies have pointed out that TiN dendrites possibly improve titanium and its alloys wear properties . Moreover, WS2 exhibits a lamellar structure, and has a high potential of having a wider range of applications as a solid lubricant due to its higher thermal stability (approximately 100 °C higher than that of MoS2) . Tushar Banerjee et al. used pulsed magnetron sputtered tech to prepare WSx reinforced tribological property of TiN coating, it showed maximum adhesion and outperformed its counterparts in maintaining low friction coefficients with less fluctuations as well as least wear rate. However, WSx exist decomposition and evaporation problems. And laser cladding also exists some problems (splash, decomposition and vaporization) when using WS2, MoS2, CaF2, BN or other solid lubricating additives, which would lead to the lessening of self-lubricating property and limit the industrial utility of laser cladding self-lubricating composite coatings . But in the laser cladding process, in situ synthesis new lubricant phase to prepare composite coating is an effective way to solve this problem. What’s more, there are few reports on the preparation of coatings with NiCrBSi+TiN+WS2 powders by laser cladding now. TiN reinforced Ni matrix composite coating with in-situ synthesized TiS lubricant phase were fabricated on Ti- 6Al-4V alloy by laser cladding with NiCrBSi, TiN and WS2 powder mixtures. The phase compositions, microstructure, microhardness and tribological behaviors are investigated by X-ray diffractometer (XRD), scanning electron microscope (SEM) with energy dispersive spectrometer (EDS) as well as a multi-functional Tribometer. Effect of WS2 contents on the microstructure, microhardness and tribological properties were studied. And the corresponding wear mechanism was discussed. Results indicate that the hardness of the coating (about 900HV0.2) is significantly improved compared with substrate (370HV0.2). Coefficients of friction and wear rates of these coatings have been significantly reduced. Besides, laser-clad coating using the mixed powders of 50%Ni- 30%TiN-20%WS2 has good anti-wearing and friction reducing effects, and the main wear mechanisms of that are abrasive wear and micro-plowing.
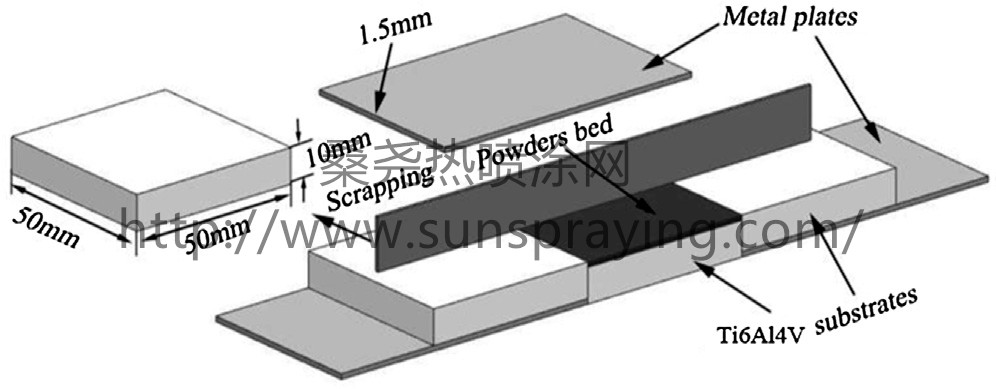
本文由桑尧热喷涂网收集整理。本站文章未经允许不得转载;如欲转载请注明出处,北京桑尧科技开发有限公司网址:http://www.sunspraying.com/
|