Cold forging represents an efficient and resource-saving technology for the mass production due to high material utilization of Ψeff = 85% and high achievable forming degrees up to φ= 0.8. These processes are characterized by high product quality, high reproducibility and short cycle times. The high forming degrees lead to high loads within the forming tools, e.g. high contact pressures up to σN= 2900 MPa which results in high tool wear. Therefore, large quantities of lubricants are currently required to ensure process reliability. In particular, the use of environmentally harmful zinc soaps and zinc phosphating as well as liquid lubricants are commonly used in industrial applications. However, due to the high demands on an environmentally friendly metal forming processes and economic reasons, there is great interest in enabling a dry forming process through alternative lubrication concepts. The application of self-lubricant coatings deposited by physical vapor deposition (PVD) on forming tools provides a solution of reduction the friction forces between the workpieces and the tools. The self-lubricating character of these PVD coatings are based on transition metal dichalcogenides (TMD), e.g. molybdenum disulfide (MoS2) and tungsten disulfide (WS2) which are widely used as solid lubricant. In such TMDs, the layers in crystallographic structure are bonded together by relatively weak van der Waals forces. This leads to low shear strength and, as a result, to a macroscopic lubricating effect. Although pure TMDs coatings deposited by PVD contributed to a high friction reduction, they cannot withstand the high tribological loads in dry cold forging processes. This attributes to their low universal hardness HU≤10 GPa and minor adhesion strength to the substrate. Furthermore, TMDs are tending to oxidize at atmosphere. In order to overcome the problems of abrasive wear, oxidization and coating delamination, TMDs must be incorporated into a hard matrix. Various coating architectures, such as hard-soft combinations, nanocomposites, multi- or nanolayer architectures, as well as different elements for the hard phase are investigated. Nitride based coating systems, as TiN and CrN are commonly used for this purpose. Another promising alternative presents the ternary system (Cr,Al)N exhibiting high hardness values up to HU = 36 GPa, good wear resistance under abrasive conditions and high chemical resistance in aggressive environments. The dcMS technology achieves higher deposition rates compared to HPPMS technology.. On the other hand, the HPPMS technology generally operates with frequencies 100 Hz ≤fpulse ≤ 4 kHz and at short pulse lengths of several tens of microseconds. Therefore, HPPMS provides high cathode peak powers e.g. PHPPMS = 316 kW, which are significantly higher than those of conventional dcMS of e.g. PdcMS = 6 kW. This leads to the deposition of coatings with a fine crystalline morphology and favorable mechanical properties. An additional advantage of the HPPMS compared to the dcMS technology is its higher capability for the uniform coating of complex-shaped tools with surfaces which do not face the target, e.g. the forming dies applied in the cold forging of steel. Investigations have shown that a hybrid process consisting of dcMS and HPPMS can combine the advantages of both technologies. Due to the high material utilization and the associated resource and energy efficiency, production processes from the field of cold forging of steel are of great importance. At present, environmentally harmful lubricants have to be used to ensure process stability as well as low wear and friction. Due to environmental, economic and legislative aspects, there is an increased research potential to reduce or to completely substitute lubricants. To achieve the goal of lubricant free dry cold forging of steel, physical vapor deposition (PVD) coatings with selflubricating properties are applied on forming tools. Promising for this application are PVD coatings on the basis of a (Cr,Al)N hard phase with embedded molybdenum and sulfur which simultaneously meet the requirements of high wear resistance and friction reduction. In the presented work, three self-lubricating coatings (Cr,Al)N+Mo:S deposited with varying bias voltage were investigated. The hybrid PVD technology, consisting of direct current and high power pulse magnetron sputtering dcMS/HPPMS, was used for the coating deposition in an industrial coating unit. Two different steels AISI D2 (DIN 1.2379) and AISI M2 (DIN 1.3343) were used as substrate materials. The influences of substrate material and heat treatments at T =250 °C were investigated. The samples were analyzed with respect to the universal hardness HU and modulus of indentation EIT using nanoindentation. To determine the interfacial adhesion of the compound coating/substrate, Rockwell indentation and scratch tests were carried out. For the analysis of the tribological behavior, unhardened AISI 5115 (DIN 1.7131) was used as counterpart material. The influence of the elevated temperature on the friction and wear behavior was investigated by Pin-on Disk (PoD) at T= 250 °C and T =23 °C. The wear of the basic bodies as well as the counterparts were analyzed by confocal laserscanning microscopy. The investigations have shown that the high temperature has a significant influence on the friction and wear behavior. The wear rate of the counterparts decreases by up to a factor greater than x=100 compared to the test at T=23 °C. Furthermore, the wear rates of the basic body of the uncoated reference specimen increase rapidly at tribological stress at high temperatures. The examined coatings exhibit high wear resistance at elevated temperatures. The contact surface was studied by Raman spectroscopy after the tribological tests. PoD tests have shown, that the applied coatings led to a significantly reduction in friction most likely due to the tribo-chemically induced formation of selflubricating MoS2 reaction layers.
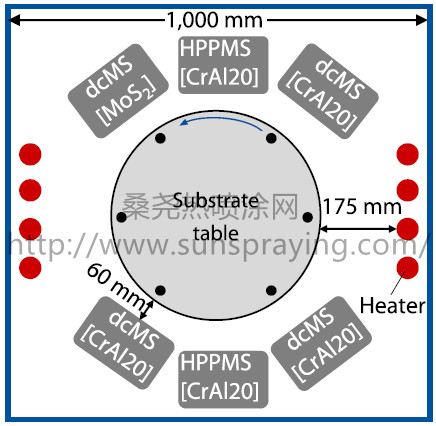
本文由桑尧热喷涂网收集整理。本站文章未经允许不得转载;如欲转载请注明出处,北京桑尧科技开发有限公司网址:http://www.sunspraying.com/
|