Au coatings are commonly used as contact materials to ensure stability and low contact resistance upon sliding contact in the electronics industry . Soft Au which is not alloyed is one of the best metals with a high electrical conductivity, and it shows excellent corrosion resistance under most working conditions. However, the low hardness of soft Au coatings leads to a low wear resistance and constrains their lifetime under applicable conditions involving intensive sliding movement . In high-reliability systems, high-performance Au coatings are required, and alloying Au with a small amount of other metal elements, such as Co and Ni, can generate harder Au coatings which exhibit distinct performance improvement . Hard Au coatings are generally obtained from acidic-cyanide baths in which nickel or cobalt salts are added as the hardening/brightening agents. Although Au-Ni and Au-Co alloy coatings exhibit a higher wear resistance compared to soft Au, adding solid lubricant materials into alloy coatings is beneficial for decreasing the wear rate by minimizing the adhesive wear. Considering the high electrical conductivity requirement of coatings, carbon (C) nanomaterials are the most suitable solid lubricants. Recently, interest in compounding metal matrices with low dimensional C nanomaterials such as C nanotubes and graphene, by electroplating to improve their mechanical and chemical performance has been increasing. The results showed that strengthened by C nanomaterials, the corrosion resistance and wear resistance of the metal coatings are improved significantly. However, considering the high toxicity of a cyanide bath and the practical difficulties of preventing agglomeration of nano-particles in Au plating electrolytes to achieve a good particle suspension and uniform coating, magnetron sputtering is an attractive alternative technique for hard Au-based C composite coating deposition.Amorphous C (a-C) including diamond-like C (DLC) with significant fraction of sp3 bonds and graphite-like C (GLC) with a high content of sp2 bonds, has been widely researched as hardening or solid lubricant particles for the production of protective composite coatings by magnetron sputtering. a-C lubricated TiC and WC sputtered coatings show a higher wear performance and significantly lower wear rates compared with pure coatings. TiN/a-GLC and silver-doped DLC coatings have been evaluated as biomaterials which exhibit a low coefficient of friction (CoF) and excellent hardness. Me–DLC (Me: W, Mo, Nb, and Ti) co-deposits have been investigated and they show good adhesion performance on substrates and an ultralow CoF of 0.03. However, there are almost no studies that have evaluated the performance of hard Au coatings compounded with a-C nanoparticles. The results would be interesting for directing advanced function coatings development with integrated wear and electrical performance. Compounding Au-Ni with carbon (C) lubricants is a feasible approach to improve its mechanical properties and wear performance. In this study, 3.5 μm-thick Au-Ni/C nanocomposite coatings with a low residual stress on CuCrZr substrates by magnetron sputtering were developed. Face-centered cubic and hexagonal close-packed stacking structures were both confirmed in the composite coatings based on transmission electron microscopy and X-ray diffraction analyses. Amorphous C (a-C) was confirmed to be the structure of C in the composite coatings, and its graphitization transition with an increase in the C content was validated by X-ray photoemission spectra and Raman spectroscopy. By compounding 0.88 wt% a-C, the hardness of the Au-Ni/a-C coating reached 400 HV, which is twice higher than that of the Au-Ni coating. The electrical resistivity of the Au-Ni/a-C coating is relatively stable with an increase in the a-C content. As graphitization occurred on the wear track, the produced composite coatings showed a minimum wear rate of 2.2×10−6mm3/N·m under atmospheric conditions, which is half that of the Au-Ni reference coating. Under vacuum, the wear performance of the produced Au-Ni/a-C composite coatings was similar to that of the Au-Ni reference coating.
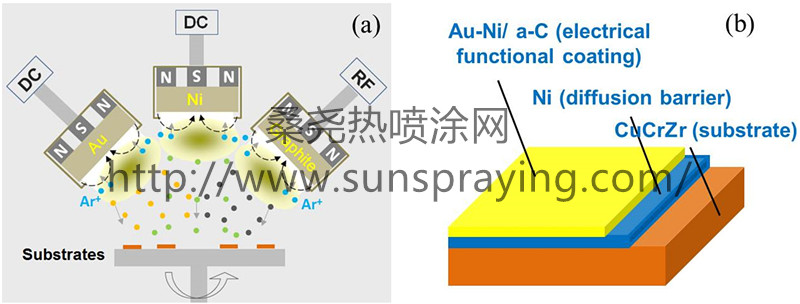
本文由桑尧热喷涂网收集整理。本站文章未经允许不得转载;如欲转载请注明出处,北京桑尧科技开发有限公司网址:http://www.sunspraying.com/
|