The efficiency of thermal power plants can be improved by increasing steam temperature and pressure. The actual ultra-supercritical (USC) power plants achieve efficiencies of approximately 45%. For this purpose, the use of advanced materials as the new generations of low-alloyed steels (T23 or T24) has become indispensable in this sector. In particular, T24 steel is presented as an advanced variant of T22 steel, due to the presence of new alloying elements and micro-additives such as V, Ti, N, and B. This steel is characterized by superior high-temperature strength and creep behavior, proper weldability and forming flexibility compared to other low-alloyed steels. However, its maximum service temperature is still less than 575 °C according to ASME Code Case 2540. It is expected that the future advanced ultra-supercritical (A-USC) power plants will work at 700°C or above, and their efficiency will increase to more than 50%. In this context, improved materials with adequate strength and resistance to high temperature will be required to withstand the higher steam parameters of these power plants. To achieve this goal, the use of materials with higher creep strength, such as Ni-base alloys, becomes mandatory. In the last decades, some alternatives have been proposed to reduce investment costs and to limit the use of Ni-base alloys. In this context, the use of coatings with high temperature resistance is the best alternative according to many studies. In particular, High Velocity Oxy-Fuel (HVOF) technique has demonstrated the ability to obtain coatings with the optimal properties. If it is compared with plasma spray technique, HVOF process produces dense coatings with a lower amount of porosity and oxidation due to the higher velocity and lower temperature of the particles in the flame. Most of these investigations in which the HVOF technique is used are focused on the deposition of coatings on flat sheets. Nonetheless, in thermal power plants, the elements that are exposed to the highest temperatures have usually tubular section, as the heat exchanger tubes. However, the use of HVOF technique for the deposition of coatings on tubular sections has not been sufficiently studied if it is compared with the deposition of coatings on flat sheets. In this context, some additional parameters need to be optimized. Therefore, one of the objectives of this research has been the optimization of HVOF parameters for its application on tubular sections, and the analysis of these parameters in the final properties of the coating. Otherwise, Ni-base alloys are presented as good candidates to be sprayed by HVOF for the protection of this type of low-alloyed steel. In particular, Ni20Cr alloy powder has been designed to produce coatings resistant to oxidation and corrosion by gases at temperatures up to 900 °C. However, this temperature depends largely on the quality of the deposited coatings. This investigation deals with the deposition of Ni20Cr coatings on the surface of T24 steel pipes using High Velocity Oxy-Fuel (HVOF) technique to improve the high temperature oxidation performance. The main parameters of the thermal spraying process as tube rotational speed, spraying distance, number of layers, gun speed over the tube surface or H2/O2 relation have been studied and optimized. The best parameters have been selected through the analysis of coating properties, employing six spraying conditions. The optimized parameters provided a homogeneous and fully dense coating with very low oxide content (4 ± 1 vol%), thickness of at least 260 ± 20 μm, micro-hardness around 460 ± 30 HV0.1, and adhesion strength higher than 29 ± 7 MPa. Thermal tests have been used to analyze the oxidation protection effectiveness of the coating at high temperatures. The optimized coating provided useful high temperature protection to T24 steel pipe up to 750 °C, while the uncoated steel only withstands up to 600 °C. After the exposure of the uncoated sample to 650 °C for 360 h, the oxide layer formed on the surface had more than 120 μm of thickness. However, in the coated samples exposed at 650 °C and 750 °C, no degradation of T24 substrate has been found. Thin layers of 1 μm (in the coating exposed at 650 °C) and 5 μm (in the coating exposed at 750 °C) of protective Cr2O3 and NiCr2O4 oxides have been observed on the external surface of the coatings.
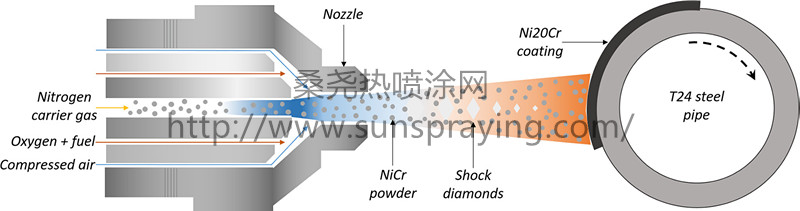
本文由桑尧热喷涂网收集整理。本站文章未经允许不得转载;如欲转载请注明出处,北京桑尧科技开发有限公司网址:http://www.sunspraying.com/
|