Deposition of hard thin films with a few microns in thickness is a common technology to improve the performance of tools, dies, and molds for many different applications . Starting with thermally activated chemical vapor deposition (CVD), different methods have been developed including plasma-assisted physical vapor deposition (PVD), plasma-assisted chemical vapor deposition (PACVD) and laser-assisted methods like pulsed laser deposition (PLD). The importance of wear-resistant hard coatings is given by the following facts. About 90% of all indexable inserts for metal cutting, based on cemented carbide substrates, are coated for wear protection by CVD or PVD techniques, with PVD being used in about 25% of the cases. The important issue for the future is not which deposition technology is used, but instead which properties can be achieved at which production cost. This is where the need for microstructural design enters the field.
Hard coatings prepared by various deposition techniques and conditions exhibit the widest variety of microstructures among materials in terms of grain size, crystallographic orientation, lattice defects, texture, and surface morphology as well as phase composition. The recent review by Petrov et al. clearly shows the microstructural evolution during film growth. Examples of the wealth of microstructures encountered in hard coatings Fig. 1 is a bright-field cross-sectional transmission electron microscopy (TEM) image of the center portion of a TiN film prepared by magnetron sputtering. The film exhibits a columnar microstructure with elongated grains, which is the typical product of today’s coating processes of ceramic materials. For characterization of the ion bombardment conditions, which are commonly used to adjust the film microstructure during plasma-assisted growth, the incident ion/metal flux ratio Jion/Jme and ion energy Eion are used as main parameters. Jion and Eion can be determined using Langmuir-probe measurements following the procedures described in Ref. The incident metal flux Jme is estimated based upon measured deposition rate values R, film composition, film thickness, and film density. Details about the evaluation and calculation of Jion/Jme and Eion are described in Refs.
In the deposition of compounds, a reaction, mainly at the substrate surface, occurs between their components, which may be introduced into the growth chamber as a gas or vapor. If all components of the films are generated by a vaporization of the target material in an inert atmosphere, these processes are generally termed non-reactive. Reactive processes involve the introduction of additional ‘reactive’ gases (such as N2, O2, CH4, etc.) into the growth chamber (here dissociation of these gases into atomic or ionic state is necessary). This differentiation is useful, but there are of course also reactions (mainly at the substrate surface), which form compound layers by ‘non-reactive’ processes. Plasmas can be used to provide heat to the film surface to improve adhesion as well as structure and to increase reactivity. A comparative study on reactively and non-reactively grown TiN films is given in .
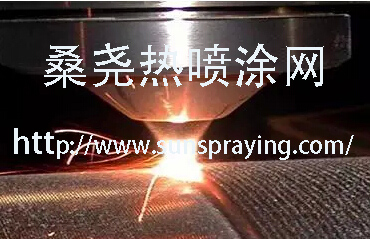
本文由桑尧热喷涂网收集整理。本站文章未经允许不得转载;如欲转载请注明出处,北京桑尧科技开发有限公司网址:http://www.sunspraying.com/
|