A series of tests was performed to identify the maximum operating temperature of coatings A and B. Substrate samples were made of Inconel X-750 foil (51 mm!19 mm!0.15 mm) and coated with the two coatings (two foils each). Coating thickness for all samples ranged from 25 to 38 mm. The coated foil samples were then divided into two batches and spotwelded to a thicker Inconel X-750 sample holder. The sample foil holders were placed in an oven and exposed to a chosen elevated temperature for 3 to 9 h at a time. Up to four thermocouples were used to monitor the temperature of each foil and to ensure that correct temperatures could be obtained for each coated foil. It was concluded that coatings A and B have similar maximum operating temperatures of about 370–385 ℃. All coatings remained in very good condition after exposure to this temperature range for several hours. Exposure of the coatings to about 400℃, however, caused coating deterioration. While coating A turned into a very fine, light-gray, ash-like powder, coating B became a dark compacted powder, which was easily removed by light rubbing. Although no rigorous study was performed to determine the maximum operating temperature of coatings C and D, the conducted high-temperature wear tests (reported in the following section) indicate that these coatings can successfully operate at temperatures as high as 800 ℃. The influence of surface preparation on the adhesion of coatings A and B to the Inconel X-750 substrate was evaluated. Twelve sample coupons (51 mm!19 mm!0.15 mm) were cut from the same stock of annealed Inconel X-750 foil. The coupons were then heat-treated, cleaned and coated according to the following test matrix. A factorial design of experiments was used with three parameters (Table 2): heat treatment (vacuum at 10K5 Torr and inert gas), cleaning the surface (with a 320 grit abrasive paper or no abrasive paper), and cleaning by chemical etching (for 15 min in a 20% solution of nitric acid {HNO3} in water or no chemical etching). An interaction between parameters, e.g. samples treated with both abrasive paper and chemical etching, was not evaluated. All samples were cleaned with hexane just before coating. The coating adhesion on the samples was tested using the ASTM Standard D 4145—83 for bend testing. Each coated sample was mounted in a vice between two polyethylene blocks and bent to a 908 angle. After a visual inspection, the samples were bent further by hand and then flattened in the vice to the full 1808 bend. The coating adhesion was further tested by applying and removing an adhesive tape. The coating performance was judged qualitatively based on the amount of cracking and/or peeling during the test and amount of the coating removed by the adhesive tape.
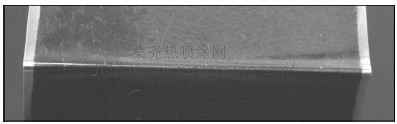
本文由桑尧热喷涂网收集整理。本站文章未经允许不得转载;如欲转载请注明出处,北京桑尧科技开发有限公司网址:http://www.sunspraying.com/
|