Further use of wear-resistant surfacing in the composition of the drill string is impossible without determining the degree of their effectiveness. For this purpose, it is necessary to conduct a comparative analysis of the wear resistance of various surfacing materials between each other and with respect to DP locks without surfacing. Comparative tests were carried out according to two tests: ASTM G65 test - the degree of resistance to abrasive wear and the Casing Wear Test - wear of the lock and casing. Tests according to the ASTM G65 test were performed on a bench with samples cut from DP locks. Samples were cut from the sleeve part of the DP. SDP 89 in the strength group G105. One series of samples was made from a serial lock, and the second series of samples from a castle With wear-resistant surfacing DRM 150 (China). As abrasive material, quartz sand with a grain size of 16 lm (or 16P) was used, which was sieved and dried in a muffle furnace. The wear of the samples was carried out by weighing on an AND GR-200 analytical balance, before and after the tests, with a maximum weighing weight of 210 g and an accuracy of 0.0001 g. Before weighing, the samples were wiped with acetone, purged with air and dried in a muffle furnace at a temperature of 60 _C. The test bench for testing the Casing Wear Test was developed based on a small-sized lathe: equipped with a frequency control system to comply with the exact and necessary speed parameters (155 rpm); equipped with a lever mechanism, providing the necessary parameters for pressing the surfacing sample to the casing pipe; the drilling fluid samples were supplied to the contact zone (density 1050–1080 kg /m3) and the presence of abrasive particles in it at the rate of 20 g per 1 L of drilling fluid. Improving the efficiency of drilling oil and gas wells is impossible without increasing the durability of the drill pipe. The main reason for drill pipe tool joints to wear in the open hole is the presence of a hard layer in aggressive geological formations and wear due to friction with the inner wall of the casing. One of the effective methods for increasing the wear resistance of drill pipes is surfacing of the drill joint of the drill pipe with cored wire (hardbanding). Leading oil and gas companies, as well as specialized companies for drilling wells, widely use surfacing materials of various grades. To assess the quality of drill pipe tool joint surfacing, in accordance with the recommendations of the American Petroleum Institute (USA), two test tests were determined: ASTM G65 abrasion resistance degree and Casing Wear Test. Studies conducted to increase the wear resistance of drill pipe tool joints and casing with wear-resistant surfacing material DRM-150 (China) applied to the material in relation to the production tool joints material testify to the efficiency of surfacing. The results of metallographic studies indicate the formation in the deposited layer of gradient layers of metal with high hardness on the surface of 650 HV0.1 to a depth of 3.2 mm, a transition zone of hardness 350 HV0.1 and the starting metal 300 HV0.1. The wear resistance of the DRM-150 surfacing is almost three times higher compared to the wear of the material without surfacing (ASTM G65 test) and more than 5 times higher than the wear resistance of the initial samples without surfacing (Casing Wear Test).
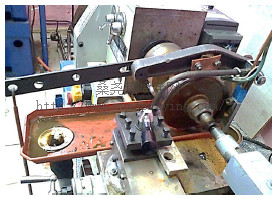
本文由桑尧热喷涂网收集整理。本站文章未经允许不得转载;如欲转载请注明出处,北京桑尧科技开发有限公司网址:http://www.sunspraying.com/
|