Composite coatings are widely applied to mechanical components due to their high mechanical, chemical and tribological properties, as well as excellent corrosion resistance. For examples, Sun et al. prepared Ni-Al2O3/graphite composite coatings on LY12 aluminum alloys using a three-step process that involved electrophoresis and electrodeposition. They found that the new Ni-Al2O3/graphite composite coatings presented excellent lubricating properties and wear resistance due to the effects of graphite and Al2O3 particles. Liu et al. prepared a Cu2O–CoO/Al2O3 composite coating on an aluminum substrate by MAO in a phosphate electrolyte modified with Cu(Ac)2 and Co(Ac)2 solutions. The catalyst exhibited an excellent chemical stability with negligible leaching ions. Furthermore, composite coatings containing fine particles of graphite, SiC, Al2O3, Si3N4 etc. can remarkably reduce the friction coefficient as well as the wear rate of the mechanical components. However, the binding modes of the substrate and composite coatings via EPD, electrodeposition, and spraying etc. include epitaxial growth, chemical bond combination, molecular bond, and mechanical bond etc., which are difficult to satisfy the requirement of pistons working conditions. MAO is a kind of surface treatment technology including electrochemical and plasma-chemical process etc. It occurs on the surface of valve metals, such as Al, Mg, Ti, Zr, Ta, and Nb and their alloys, and forms a porous ceramic coating. The binding mode of ceramic coating and the substrate is a metallic bond combination with the highest bonding strength. In our previous study, MAO has been demonstrated to significantly improve wear-resisting, and the average microhardness is more than 1200 HV. A hardness gradient exists across the coating thickness from the dense layer to the loose layer of ceramic coating. However, the hardness of cylinder liner surface is far less than the dense layer, and the loose layer is easy to wear off due to the pores inside it. Although by MAO alone, we may increase the wear resistance at the surface of a piston made from high-silicon aluminum alloys, some measures must be taken to increase the wear resistance of cylinder liner surface, which will observably raise the costs of technology.
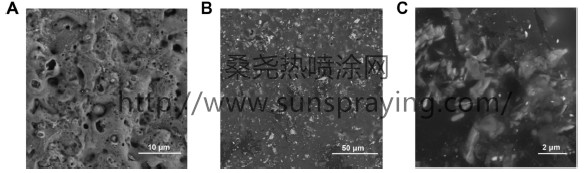
本文由桑尧热喷涂网收集整理。本站文章未经允许不得转载;如欲转载请注明出处,北京桑尧科技开发有限公司网址:http://www.sunspraying.com/
|