In traditional thermal spray processing the feedstock material can be categorized in one of these three formats: (1) a powder, (2) a metallic wire, or (3) a ceramic rod. Although metallic wires and ceramic rods played an important contribution in the thermal spray market up to the 1970s, the huge majority of feedstock materials for thermal spraying today are found in powder form. This is highly related to (1) the introduction of TBCs produced via air plasma spray (APS) as a regular product for gas turbine engines (1980s), as well as (2) the advent of high-velocity oxygen fuel (HVOF) WC-based coatings for landing gears and wear and corrosion industries (1990s). These applications are (1) among the most important ones in the thermal spray market in the twenty-first century and (2) require powder feedstock particles. As a ‘‘rule of thumb,’’ typically the majority of the feedstock powder particles exhibit diameters somewhere within the 5-100 micron scale. Depending on the feedstock material (e.g., ceramic, metal, polymer or composites) and the spraying process (e.g., APS, HVOF and flame spray), the particle size cut is tailored to achieve optimal processing conditions in order to engineer coatings for specific applications. In addition, these powder particles are fed into the spray torches by a carrier gas via a powder feeder. In the traditional thermal spraying, the fully and/or semi-molten microscopic particles impact the substrate surface or previously deposited layers at or near a 90 angle. This is due to their high inertia/momentum, i.e., they do not follow the streamlines of the thermal spray jet at or next to the coating/substrate surface, i.e., the streamlines are deviated and move across the coating/substrate surface. At the impact with the substrate surface or previously deposited layers, the particles deform via spreading, solidify, and form the coating microstructure (overlapping of arriving splats). The splats exhibit diameters varying from tens to about a hundred microns and thicknesses ranging from * 1 to few microns, thereby forming the socalled anisotropic lamellar microstructure. The coating porosity values typically range from 5 to 20% for APS and 1 to 5% for HVOF processing, although denser and more porous coatings can also be produced under controlled conditions for these processes. The minimum coating thickness to uniformly coat a given surface is considered to be * 100 microns. The majority of the coatings exhibit thickness varying from * 100 to 500 microns. But the maximum coating thickness can reach few millimeters for some specific applications. It is important to highlight the fact that particles smaller than * 5 microns in diameter cannot be properly fed into thermal spray torches via carrier gas-based powder feeders. This is mainly related to low flowability and injection difficulties of fine particles. As the particle size decreases, the surface-area-per-volume ratio of the powder increases. The higher this ratio, the higher the contact and friction among particles, i.e., their flowability is drastically reduced and they start to clog the hoses and tubing of the equipment. In addition, smaller particles cannot be injected into the core of the flame due to their lower mass. If a higher carrier gas flow rate is used, it will cause interference with the flame. Therefore, traditional powder thermal spraying is typically limited to * 5-micron particles at the lower end of the particle size cut.
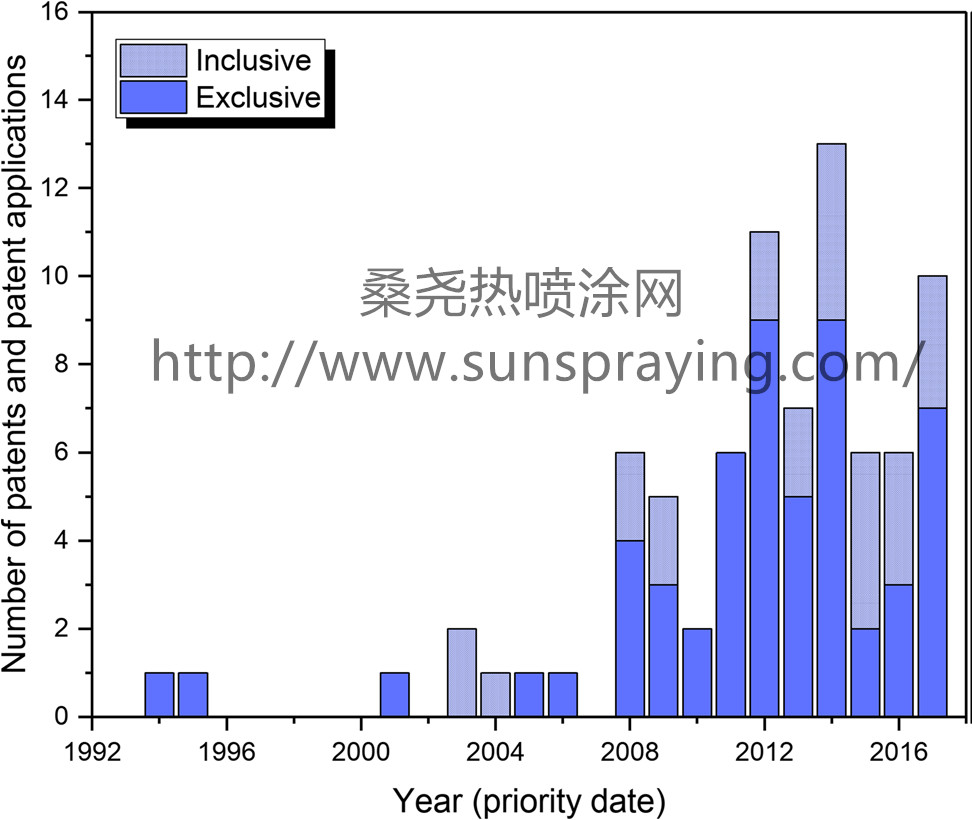
本文由桑尧热喷涂网收集整理。本站文章未经允许不得转载;如欲转载请注明出处,北京桑尧科技开发有限公司网址:http://www.sunspraying.com/
|