Titanium alloys have many advantages such as low density, high strength to weight ratio, excellent corrosion resistance and biocompatibility, etc. Thus they have been widely applied in aerospace, chemical engineering, metallurgical, medicine and nuclear industries. However, titanium alloys are limited for wear applications due to their poor tribological properties, such as high friction coefficient and prone to adhesive wear, leading to their failure in the early service stages. Surface modification and treatment of titanium alloys by using methods such as physical vapor deposition (PVD) or chemical vapor deposition (CVD), ion implantation, magnetron sputtering techniques , or laser cladding have improved the wear resistance for titanium alloys dramatically. However, the applications of these surface technologies are restricted due to the generation of some adverse effects on the titanium alloys. For examples, it is easy to cause thermal deformation of the titanium substrates by the nitriding or the sulfurizing process due to the high temperature involved. It is hard to carry out the processing for the large parts due to the necessary vacuum or gas environment for PVD. The coating deposited by the magnetron sputteringmethod is relatively thin with low efficiency, which is also difficult to obtain a surface coating with large thickness and high bonding strength. The instrumentation and equipment of laser cladding are complex and expensive and it is difficult to achieve the coating on titanium alloy with complex geometry. Therefore, it is necessary to prepare excellent anti-wear coatings on titanium alloys, which will obtain a metallurgical bond with titanium substrate while minimizing the total heat input into the titanium substrate to avoid thermal deformation. Electrospark Deposition (ESD) is a typical surfacemodification technology with high energy density and low heat input, which has been widely used in the preparation of modified strengthening coatings. Utilizing the high energy pulsed discharge between electrode and metallic substrate, the ESD process can deposit the melting electrode materials onto the substrate by accomplishing metallurgical bonding between the materials and the substrate. By now, several coatings have been achieved on titanium alloys by ESD process. Wang et al. [19] depositedWC92-Co8 coatings on titaniumalloy by the ESD and they studied the microstructure and interface of the coatings. Themicrohardness of the coating reached HV 1192, but the coating was relatively thin (26.3–56.12 μm) and inhomogeneous. Tang et al. carried out ESD under air, nitrogen or silicone oil conditions using a graphite electrode on titanium alloy. Their results showed that the ESD coating treated in silicone oil exhibited improved biocompatibility and biological activity in comparison with the other conditions, but the coating thickness was only 11.2–14.3 μm and the silicone oil environment restricted the application for large mechanical parts by the ESD. Hao et al. prepared TiN coating on TC4 titaniumalloy by ESD, but the coatingwas relatively thin (12.1–24.3 μm) andwithmany defects such as micro-cracks and holes. Due to the good wear resistance, high temperature resistance, high corrosion resistance and other excellent properties of ceramic coatings, the authors have previously prepared TiN ceramic coatings on TC11 titanium alloy by ESD. The ceramic materials are highly brittle and their fracture toughness is low, and many defects such as micro-cracks and holes may exist in the coating. Though the ceramic coating can improve the wear resistance of titanium alloy in low loading friction conditions, it is limited to great improvement of wear resistant performance under heavy friction conditions. To improve the wear resistance of titanium alloy, especially under high loading friction conditions, TiN/Zr-base amorphous-nanocrystalline composite coatings were prepared by Electrospark Deposition (ESD) on the surface of TC11. The microstructure of the coatings was examined and the fracture toughness and microhardness of the coatings were tested. The wear behavior and mechanism of the coatings under various loading conditions were investigated. The results show that the composite coating consists of two parts, one is a TiN substrate coating (coating I) and the other is Zr-base amorphous-nanocrystalline surface coating (coating II). The former is mainly composed of TiN and Ti2N phases while the latter is mainly composed of amorphous phases,within which a large number of nanoparticles exists with diameter between 2 nm and 4 nm. These nanoparticles mainly include CuZr2, Ni2Zr3, and NiZr2, etc. The composite coatings are dense and their thickness is approximately ranging from90 μmto95μm, bondingwith substrate metallurgically. The fracture toughness of composite coatings is approximately 9.36 MPa m1/2. The microhardness of the coating changes in a gradient trend. The average microhardness of coating I and coating II are 1221.5 HV1.96 and 801.3 HV1.96, respectively. The wear tests results show that the composite coatings exhibit excellent wear resistance, especially under high loading friction conditions. The mainwear mechanisms of the composite coatings are the micro-cutting wear and themulti-plastic deformation wear under low friction conditions. However, under high loading friction conditions (N8 N), the main wear mechanismof the composite coatings changed to micro-cuttingwear, accompaniedwith a portion of micro fracture wear. The average wear rate of the composite coating is approximately 1.2–1.5 times of that of the single TiN coating and 2.6–2.7 times of that of the TC11 substrate, respectively.
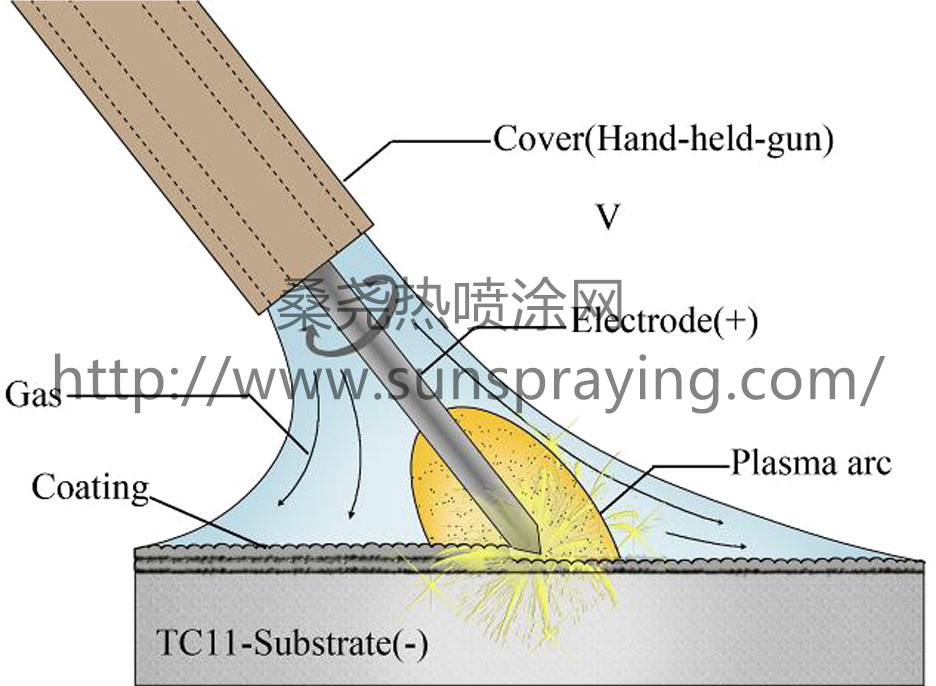
本文由桑尧热喷涂网收集整理。本站文章未经允许不得转载;如欲转载请注明出处,北京桑尧科技开发有限公司网址:http://www.sunspraying.com/
|