In marine environments, extreme corrosion occurred in all types of stainless steel, including STS 304, which can lead to serious problems if it occurs intensively in a vessel that does not have a stern tube cooling system on the surface of the propeller shaft in the stern tube, or in the clearance between the stern tubes and the surrounding wood. Comprehensive investigations have been performed to determine an appropriate corrosion countermeasure. Attempts have been made to protect stainless steel shaft systems from corrosion by installing grounding plates on the hull or using anticorrosive paint. However, the problem still exists and a definitive alternative technology has not yet been established. Pitted and cracked shafts must be repaired in dry docks by grinding and welding. Differences of opinion often exist between an inspector certifying the repairs and the companies performing the repairs due to ambiguities in the regulations. The thermal spraying coating materials for the corrosion protection are Al, Zn and Zn-15% Al. In the previous investigation, the Al thermal spraying coating material presented the best corrosion protection characteristics. Therefore, in this work the effects of Al coating thickness were evaluated with the point of microstructure and electrochemical property. Fig. shows the surface and cross-section morphologies with different thermal spray coating thickness. Plate shape was observed at surface microstructure of zinc coating material. The reason is that solidification occurs while molten metal particle of high velocity clashes base metal surface and crushes it. The reason why thermal spray layer forms is due to the specific characteristics of plate accumulation structure and formation of large porosity because of incomplete plate accumulation, and melted particle by flame of high temperature at thermal spray spreads platy or radial shape after clashing base metal with high velocity. After that, small particle is separated in the thin and unstable end part, and porosity of middle size is formed, when the plate is made while melting particles strike solidified particle in the end of splat. In addition, while plate was made from the process that gas isolated in melting particle strikes base metal in the flame of high temperature, small porosity is formed inside when gas evaporates. Because of existing many groove, the corrosion resistance is decreased due to the porous coating layer. The coating layer thickness affects largely the corrosion resistance. Fig shows the EDX composition distribution of Al coatings with different thickness. Because aluminum coating materials were used, the aluminum distribution was considerably observed in coating layer and porous shapes was also observed inside aluminum coating. It is considered that other impurities affect the result because tendency of oxygen was not observed remarkably in porous part. Moreover, Cr was considerably observed which is included in base metal. Therefore, the coating formation is observed by the composition distribution of Cr and Al. In the observation of cross-sections, the laminated microstructure at the coating layer with different thickness was presented. The surface in the case of 90 μm thickness was rough. Overall, similar tendency appeared according to the thickness, but the porosity increased with thickness increasing. In general, the Zn and Al content in the coating layer is known to be approximately 5%−10%. Even though base metal was exposed to seawater environment due to defect like porosity or oxidized substance, base metal could be protected from corrosion. Thermal spray coating brings out sacrificial characteristics if micro-cell forms, because base metal with electrochemically high potential operates as cathode and thermal spray coating layer showing low potential operates as anode. This corrosion protection function is available in the case that thermal spray coating acts as sacrificial anodic. Therefore, the thickness absolutely affects the durability of base metal.
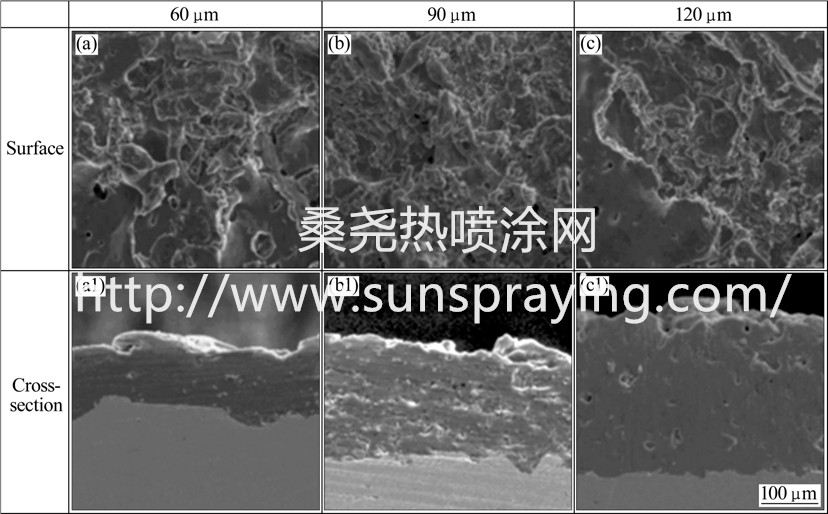
本文由桑尧热喷涂网收集整理。本站文章未经允许不得转载;如欲转载请注明出处,北京桑尧科技开发有限公司网址:http://www.sunspraying.com/
|