Chromium plating is the most used electrodeposited coating to obtain high levels of hardness, resistance to wear and corrosion and a low coefficient of friction for applications in the aerospace, automotive and petrochemical fields. Chromium plating properties, such as hardness and microcrack density, change with the bath composition, current density, bath agitation, temperature, etc. Among other things, a significant characteristic of chromium electroplating is the high tensile residual internal stresses originating from the decomposition of chromium hydrides during the electrodeposition process. These high tensile stresses in electroplated chromium coatings increase as thickness increases and are relieved by local microcracking during electroplating. Therefore, basically, microcrack density is related to the high tensile residual internal stresses, hardness, and corrosion resistance. It was observed that the residual stresses through-thickness decrease with the depth of the coating and increase again at the coating_substrate interface. Bending fatigue tests on samples with different coatings and coating conditions indicate that the fatigue strength is dependent on the fracture behavior of the substrates and on the hardness and residual stresses at the substrate surface. It was also observed that the hard chromium electroplating reduces the fatigue strength of a component. Due to this fact, the design of hard chromium plated components, which are subjected to dynamic loads, may consider this negative influence to guarantee safety during operation. Therefore, the use of effective methods to improve the fatigue strength shall be considered. Shot peening is a well-known process to increase fatigue life of structures subjected to constant and variable amplitude loading. The compressive residual stress obtained by surface plastic deformation is responsible for the increase in fatigue strength in shot peened mechanical compo- nents. Compressive residual stresses induced by machining processes are also responsible for the improvement in fatigue resistance of AISI 4340 steel. Increase in the fatigue crack propagation resistance in AISI 4340 steel with electron beam surface hardening was associated to residual stress distribution and microstructural characteristics. However, problems concerning chrome plating, such as health and environmental hazards, increasing costs and a performance not in accordance with the specifications, have resulted in a search to identify possible alternatives. Aircraft landing gear manufacturers are considering tungsten carbide WC. Thermal spray coatings applied by the high velocity oxy-fuel HVOF. process as an alternative to hard chrome plating. The question to be answered is if the performance of the alternative candidate is at least comparable to results obtained for hard chrome plating. Comparisons of experimental data showed better corrosion resistance for several HVOF coatings with respect to chrome plating. In the case of fatigue and friction tests, the results were acceptable, indicating interesting perspectives on the use of tungsten carbide coating to replace chrome-plating. Analysis of the wear performance of tungsten carbide coated samples in the presence of air, aqueous and aqueous abrasive media indicated better results in terms of volume loss and change in surface roughness than for the mild steel substrate. The objective of this research is to compare the influence of the tungsten carbide thermal spray coating applied by HP_HVOF and hard-chromium plating on the fatigue strength, abrasive wear and corrosion resistance of AISI 4340 steel. S_N curves were obtained in rotating bending and axial fatigue tests for the base material, chromium plated, and tungsten carbide coated specimens. The effect of tungsten carbide thermal spray coating applied by HP_HVOF process and hard chromium electroplating for the rotating bending and axial fatigue tests was to decrease the fatigue strength of AISI 4340 steel. The influence is more significant in high cycle fatigue tests than in low cycle fatigue tests. The decrease of the fatigue strength was higher in chromium electroplated specimens than in tungsten carbide coated specimens. The higher rotating bending fatigue strength of the conventional hard chromium in comparison to the accelerated hard chromium electroplating, despite the higher thickness of the former, is associated
with the lower microcrack density of the conventional hard chromium electroplating. _ A small increase in rotating fatigue strength was obtained for tungsten carbide thermal spray coated specimens blasted with aluminium oxide in comparison to samples without superficial treatment. No change in the microstructure of the base metal due to deposition process was observed for tungsten carbide thermal spray coating applied by HP_HVOF process and for chromium electroplating. _ For axial fatigue tests, the negative influence of coatings on the fatigue strength of the steel followed the same tendency observed in rotating bending fatigue tests. Analysis of the hard chromium electroplated results revealed that the different microcracks density did not play an important role in their performance. The wear weight loss tests showed better results for the HP_HVOF tungsten carbide coating in comparison
to the chromium electroplating. An initially higher wear weight loss for the accelerated hard chromium electroplating occurred, decreasing continuously with the increase in test cycles._ Both coatings completed the test of 72 h with full corrosion. For the HP_HVOF tungsten carbide coating, a better corrosion resistance was observed after sealing application before testing. With respect to both hard chromium electroplated samples, the results indicate clearly the higher salt spray resistance of the accelerated hard chromium electroplated specimens.
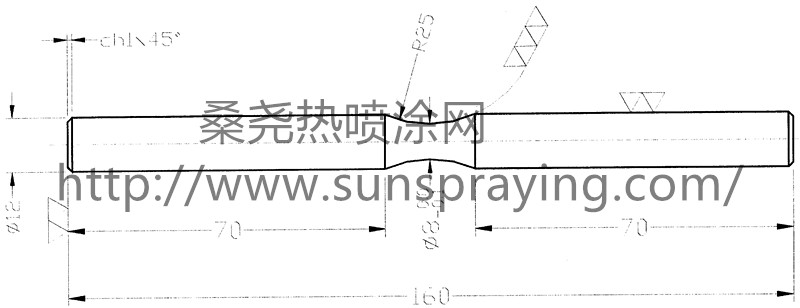
本文由桑尧热喷涂网收集整理。本站文章未经允许不得转载;如欲转载请注明出处,北京桑尧科技开发有限公司网址:http://www.sunspraying.com/
|